Является инновационной технологией для сушки и измельчения материалов: производства пеллет и брикетов, древесно-полимерных композитов, пористого кирпича, жидкого биотоплива, химически чистых растворителей и лекарств.
1.1. Причина и история создания.
Общеизвестно, что:
а) измельчать легче (эффективнее) влажную древесину (биомассу), нежели сухую;
б) сушка материала тем эффективнее, чем сильнее он измельчен.
Из этих двух аксиом неоспоримо следует, что материал сначала нужно измельчить, а потом только сушить, и никак не наоборот. Тем не менее, весь мир делает именно наоборот. Почему? Причин две:
1) раньше не принято было экономить энергию;
2) вследствие слипания влажного измельченного сырья очень трудно организовать разгрузку измельчающих машин (дробилок) и транспортировку этого сырья к сушильному агрегату. Вторая причина делает практически невозможной работу такой схемы в условиях суровой российской зимы. Таким образом, поменять последовательность операций оказалось практически невозможным. В мае 2005 года на предприятии-изготовителе очень кстати получили результат одного своего эксперимента - эффект высушивания сырья при пропускании его через молотковую дробилку без применения тепла. Совершенно естественно, что в результате анализа этого эффекта и с учетом постулатов, описанных выше, автор пришел к выводу о необходимости объединения процессов сушки и измельчения сырья - в одном устройстве.
Основные чертежи агрегата были изготовлены в марте 2006 года. Промышленный образец АС-1 изготовлен и запущен в начале октября 2006 года.
В 2008г. был запущен в серийное производство АС-2.
В январе 2009г. завершены производственные испытания и запуск в серийное производство АС-3.
В конце 2009г. началось серийное производство последнего поколения АС-4.
1.2. Аналоги.
Перед началом проектирования агрегата было решено установить наличие мирового опыта создания такого оборудования. Оказалось, что эффект сушки при измельчении сырья известен как минимум с 1926 года. Установки, использующие данный принцип, более 15 лет делаются в Англии и Германии. Принцип действия этих установок одинаков – тепло вместе с сырьем подается в дробилку (молотковую или штифтовую мельницу). Однако эти установки обладают как минимум тремя огромными недостатками:
1) энергетическая эффективность этих установок очень низка вследствие изначально низкого КПД молотковых и штифтовых мельниц;
2) в виду отсутствия динамического классификатора и невозможности применения сит - процесс регулировки степени измельчения и сушки сильно затруднен, в результате - эти устройства либо плохо измельчают, либо плохо сушат.
3) ввиду высокой интенсивности протекания тепломассобменных процессов конструкция этих устройств очень сложна, это приводит к их высокой стоимости и высоким эксплуатационным затратам.
4) процесс замены мелющих органов очень сложен и приводит к большим затратам времени, как следствие - эти устройства имеют крайне низкий коэффициент использования.
5) в силу конструктивных особенностей молотковых и штифтовых мельниц данные установки чрезвычайно чувствительны к наличию в сырье посторонних примесей – камней, металла и т.п.
1.3. Общее техническое описание.
Конструктивно АС представляет собой стальной цилиндр (АС-1 и АС-2) либо параллелепипед (АС-3 и АС-4), внутри которого расположен высокоскоростной активатор и специальные направляющие. Движение сырья внутри агрегата организовано таким образом, что частицы обрабатываемого материала испытывают удары активатора и множественные взаимные встречные соударения. Эти многократно повторяющиеся соударения и взаимное трение приводят к измельчению и одновременному нагреву сырья, что, в конечном счете, приводит еще и к его высушиванию.
Для удерживания сырья в рабочей камере до момента достижения необходимой влажности или размера частиц служит специально разработанная система динамической классификации сырья. Отделение системы от внешней среды осуществлено двумя шлюзовыми затворами. Таким образом, регулировка степени сушки/измельчения производится с пульта управления без остановки агрегата.
Производительность зависит от влажности и размера частиц сырья на входе, необходимой конечной влажности и степени измельчения материала. При подаче в агрегат горячего воздуха производительность увеличивается. Номинальная расчетная производительность четырех модификаций - от 0,5 до 3 т/час.
Сырой материал (опилки и/или щепа естественной влажности, торф и т.д.) подается в агрегат сушки/измельчения АС. Нагретый с помощью теплогенератора воздух в необходимом количестве также подается в АС и участвует в процессе сушки. На выходе АС измельченная и высушенная до необходимой влажности фракция осаждается в циклоне, отработанный теплоагент через дымосос отводится наружу.
АС-3. Технологическая схема
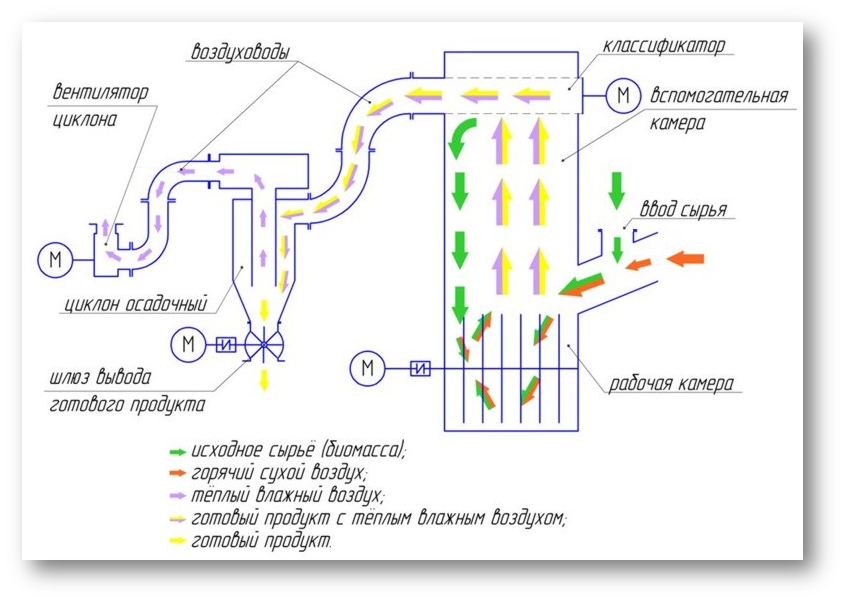
1.4. Недостатки.
Известен только один – необходимость организации предварительного сепарирования сырья.
1.5. Преимущества перед линиями сушки-измельчения, основанными на сушильном барабане.
1) Высочайшая энергетическая эффективность и, как следствие, – экономичность. При производительности около 1 т/час (по сушке-измельчению древесной щепы) мощность главного двигателя - 75 кВт, суммарная мощность остальных 3 двигателей - 29 кВт. Реальная потребляемая мощность - около 70 кВт !!!
2) Возможность точного регулирования конечного размера частиц измельчаемого материала и их влажности.
3) Высокая степень автоматизации, легкости регулирования и поддерживания заданных параметров процесса сушки-измельчения.
4) Меньшее количество элементов оборудования и, как следствие, – большая надежность.
5) Максимальная пожаробезопасность.
6) Максимальная компактность (АС производительностью 1 т/час без теплогенератора занимает всего 6 м2) и, как следствие, – намного меньшие расходы на здания, фундаменты, транспортные расходы и т.п.
7) Максимальная заводская готовность – низкие затраты на монтаж (занимает несколько часов рабочего времени).
8) Низкие эксплуатационные расходы ввиду минимального количества изнашиваемых деталей.
9) Минимальное время простоя при замене быстроизнашиваемых деталей.
10) Максимальная легкость обслуживания.
11) Большая пластичность готового продукта, увеличивающая производительность линии гранулирования (брикетирования) и уменьшающая износ узлов прессования !!!
12) Возможность изготовления мобильного (контейнерного) варианта установки.
1.6. Использование.
1.6.1. Сушка и измельчение биомассы в производстве твердого биотоплива (топливных гранул и брикетов).
1.6.2. Сушка и измельчение биомассы в производстве древесно-полимерных композитов (ДПК, “древопласт”).
1.6.3. Сверхтонкий размол древесины и других растительных материалов в процессе производства жидкого биотоплива, растворителей (биобутанола, ацетона и т.д.) и водорода.
1.6.4. Приготовление из практически любой биомассы (отходов древесины, лигнина, торфа, сельскохозяйственных отходов, в т.ч. навоза) сухой мелкодисперсной муки для дальнейшего высокоэффективного сжигания в пылевых горелках котельных, электростанций и ТЭЦ.
1.6.5. Сушка и сверхтонкое измельчение трав и другого растительного сырья в фармацевтике (в процессе производства лекарств это в десятки раз увеличивает скорость и эффективность экстракции, мгновенная и низкотемпературная сушка обеспечивает максимальную сохранность полезных веществ).
Совершенно очевидно, что с такими преимуществами АС просто обязан сделать революцию не только в бизнесе по производству топливных гранул из биомассы, но и в технологиях сушки/дробления в целом.
1.7. Некоторые цифры.
Агрегат сушки-измельчения АС появился на рынке сравнительно недавно (в 2009г.), принятию решения о его использовании препятствуют сомнения и вопросы. Поскольку все познается в сравнении, ниже приводится сопоставление АС с другими устройствами сушки-измельчения древесных отходов. Самым известным и популярным таким оборудованием на постсоветском пространстве является комплекс АВМ-1,5 (агрегат витаминной муки), ранее устанавливаемый повсеместно в колхозах, а теперь используемый для подготовки древесных отходов к гранулированию и брикетированию.
В Таблице 1 приведено сравнение энергопотребления – одного из самых важных параметров оборудования.
Таблица 1
Присоединенная электрическая мощность, кВт: | АВМ-1,5 | АС-4-1000 |
При работе от опилок | ||
Привод сушильного барабана АВМ-1,5 | 11 | - |
Привод ротора АС | - | 75 |
Классификатор АС | - | 7,5 |
Вентилятор (дымосос) | 55 | 22 |
Привод шлюзового затвора циклона | 3 | 1,5 |
Привод дробилки | 55 | - |
Вентилятор осадочного циклона | 15 | - |
Привод шлюзового затвора циклона | 1,5 | - |
Итого: | 140,5 | 106 |
При работе от крупной щепы | АВМ-1,5 | АС-4-1000 |
Привод дезинтегратора | 55 | - |
Привод транспортера | 3 | - |
Привод сушильного барабана АВМ-1,5 | 11 | - |
Привод ротора АС | - | 110 |
Классификатор АС | - | 7,5 |
Вентилятор (дымосос) | 55 | 22 |
Привод шлюзового затвора циклона | 3 | 1,5 |
Привод дробилки | 55 | - |
Вентилятор осадочного циклона | 15 | - |
Привод шлюзового затвора циклона | 1,5 | - |
Итого | 198,5 | 141 |
Как видно из Таблицы 1, АС потребляет электроэнергии меньше, чем АВМ-1,5, на 24% при работе от древесных опилок и на 29% при работе от древесной щепы.
Что это означает на практике? При работе в 2 смены (18 часов) и 22 дня в месяц, разница составит 13 662 кВт и 22 770 кВт соответственно. Таким образом, при сегодняшней стоимости электроэнергии, например, в Украине 1,05 грн (0,131$) за 1кВт/ч., использование АС в сравнении с комплексом АВМ-1,5 может сэкономить при работе от опилок 14 345 грн. (1 789 $), а при работе от щепы 23 908 грн. (2 982 $), и это только за месяц.
Возникает закономерный вопрос: за счет чего достигается экономия? Ответ прост – за счет правильно организованного процесса сушки-измельчения. Всем хорошо известно, что обрабатывать легче влажную древесину, а сушить легче измельченный материал. Именно в такой последовательности осуществляется процесс в агрегате АС, и ровно наоборот, в АВМ.
Однако, только одной экономией электроэнергии дело не ограничивается. В Таблице 2 приведено сравнение некоторых других показателей (ориентировочно)
Таблица 2
Параметр | АВМ-1,5 | АС-4-1000 |
Занимаемая площадь, минимум, м2 | 100 | 10 |
Необходимая высота здания, м | 9 | 7 |
Стоимость нового модульного здания, USD | 100 000 | 33 000 |
Стоимость фундамента, USD | 50 000 | 0 |
Транспортные расходы, руб. на 1000 км | 5 000 | 850 |
Количество электромоторов | 6 (8) | 4 |
Количество дорогих подшипников | 8 | 2 |
Необходимость частой замены сит | да | нет |
Возможность регулировки степени измельчения с пульта | нет | да |
Возможность быстрого старта и остановки | нет | да |
Пожароопасность | очень высокая | крайне низкая |
Возможность переноса завода на другое место | очень сложно | легко |
Срок изготовления оборудования, месяцев | 6 | 2 |
Срок монтажа, месяцев | 3 | 1 |
Срок пуско-наладки, недель | 4 | 1 |
Срок выхода на проектную производительность, месяцев | 3 | 1 |
Увеличение производительности дальнейшего прессования, % | 0 | 50 и более |
Необходимо обратить особое внимание на последнюю строку Таблицы 2. Сухие опилки, выходящие из АС, намного пластичнее, чем прошедшие через АВМ. В результате, брикетный пресс, обычно имеющий производительность 400 кг/час, после АС брикетирует 630 кг/час и более.
Агрегат сушки-измельчения сертифицирован.
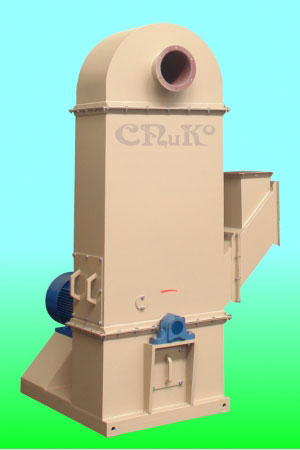
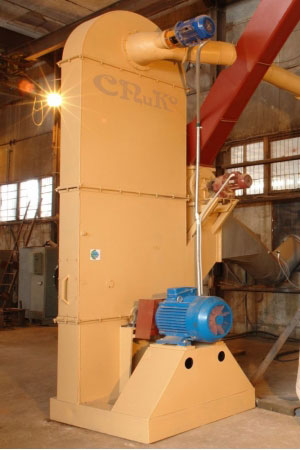
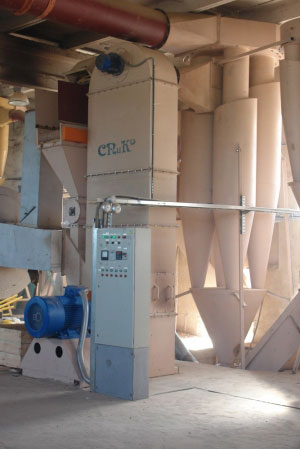
АС-4-500, 500 кг/час АС-4-1000, 1000 кг/час АС-4-300, 300 кг/час
(от щепы до частиц (от щепы до частиц (от щепы до частиц
размером ~ 3х1х0,5 мм) размером ~ 3х1х0,5 мм) размером ~ 3х1х0,5 мм)