В настоящее время распространены технологии брикетирования (производства топливных брикетов из отходов лесопереработки) без использования искусственных связующих веществ, так как в этом случае получается экологически чистый брикет. В качестве связующего при брикетировании выступает лигнин, выделяющийся из клеток древесины под действием давления и температуры.
Технологические процессы брикетирования могут включать следующие основные операции: транспортировку сырья к брикетирующей установке; измельчение крупных древесных отходов; сепарацию (сортировку сырья по размерам фракций); сушку; термообработку; прессование (формирование брикета); хранение и транспортировку к месту потребления. Следует отметить, что перечисленные операции выполняются не во всех технологических процессах брикетирования.
К топливным брикетам предъявляются определенные требования, регламентированные стандартами. В табл. 1 представлены технические требования к топливным брикетам, разработанные в России.
У кожній країні діють свої стандарти, що регламентують вимоги до твердого біопалива, наприклад, в США - Standard Regulations & Standards for Pellets in the US: The PFI; в Великобританії - The British BioGen Code of Practice for biofuel; в Швейцарії - SN 166000; в Швеції - SS 187120; в Австрії - ONORM M 7135; в Німеччині - DIN 51731 і DIN plus.
У 2011 році в Європейському союзі введені стандарти якості біопалива EN 14961-2 (табл. 2).
Резюмуючи дані, представлені в таблиці 2, відзначимо, що щільність паливних брикетів повинна бути вище 1 г / см3, вологість - не перевищувати 15%, а зольність складати 0,7-3%; в брикетах допускається вміст кори.
Оцінимо нижчу теплоту згоряння брикетів по формулі Д. І. Менделєєва:
Таблица 1. Технические требования к топливным брикетам
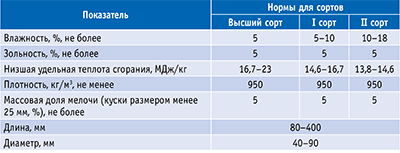
Таблица 2. Требования к топливным брикетам по стандарту EN 14961-2
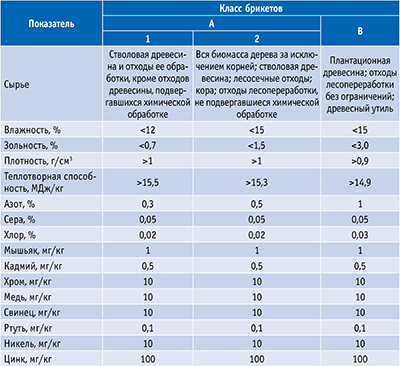
Где С - процентное содержание углерода в коре по массе, H - процентное содержание водорода, O - процентное содержание кислорода, W - относительная влажность материала брикета.
По формуле (1) при C = 42%, H = 8%, O = 50% построим график, представленный на рис. 1.
Итак, при влажности ниже 15% требование к минимальной теплотворной способности брикетов выполняется автоматически.
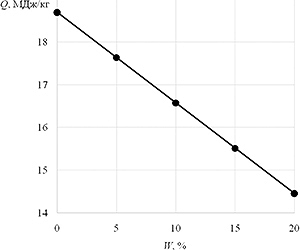
Современное прессовое оборудование для брикетирования
Основным оборудованием, определяющим производительность участка по производству брикетов, являются прессы. Известны прессы для брикетирования древесных отходов следующих конструкций: штемпельные с открытой матрицей; копровые; шнековые; гидравлические; ротационные; ударно-механические. Копровые и ротационные прессы широкого распространения не получили.
Гидравлические прессы считаются наиболее надежными и безопасными для оборудования современных высокопроизводительных брикетных станций.
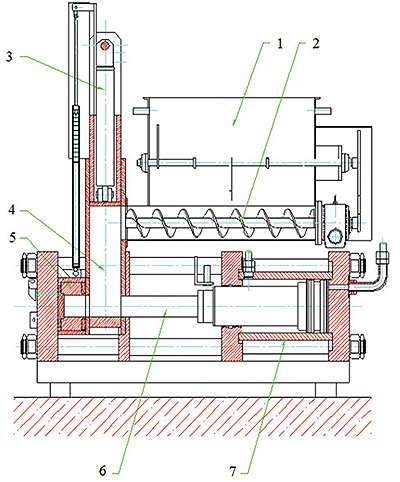
Рис. 2. Схема гидравлического пресса: 1 – бункер, 2 – загрузочный шнек, 3 – поршень наполнителя, 4 – камера наполнителя, 5 – пресс-форма, 6 – главный прессующий поршень, 7 – прессующий цилиндр
Таблица 3. Преимущества и недостатки разных конструкций прессов
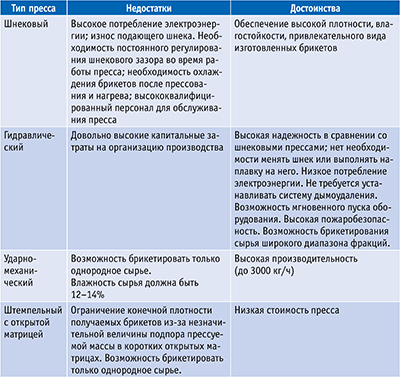
Таблица 4. Технические характеристики модельного ряда прессов фирмы RUF (Германия) Технические данные RUF 100 RUF 200 RUF 400 RUF 600 RUF 1100
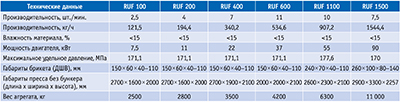
Таблица 5. Примерная оценка рентабельности продукции брикетного производства
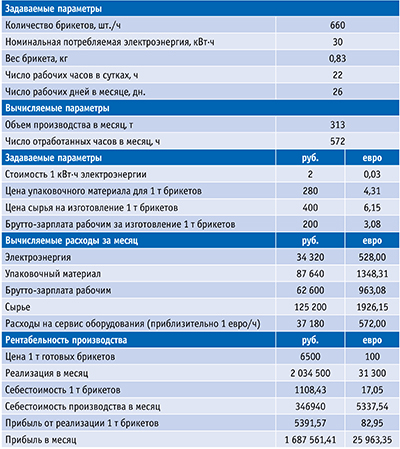
Операция брикетирования на гидравлических прессах осуществляется следующим образом (см. схему гидравлического пресса на рис. 2).
Загрузочный шнек подает материал, находящийся в бункере, в наполнитель, продолжительность работы загрузочного шнека связана с системой автоматического дозирования материала.
После окончания загрузки наполнителя и остановки загрузочного шнека поршень наполнителя выполняет предварительное сжатие материала, находящегося в камере наполнителя.
Загрузочный шнек подает материал, находящийся в бункере, в наполнитель, продолжительность работы загрузочного шнека связана с системой автоматического дозирования материала.
После окончания загрузки наполнителя и остановки загрузочного шнека поршень наполнителя выполняет предварительное сжатие материала, находящегося в камере наполнителя.
Главный прессующий поршень передвигает предварительно сжатый материал в одну из двух камер пресс-формы и сжимает материал в плотный брикет. В течение этого этапа выталкиватели, установленные параллельно главному цилиндру, выталкивают готовый брикет из второй камеры пресс-формы через специальные отверстия в передней панели.
Поршень наполнителя поднимается вверх. Загрузочный шнек начинает подачу следующей порции прессуемого материала. Прессующий цилиндр возвращается в исходное положение, пресс-форма перемещается, после чего операции повторяются.
Характеристики прессов других производителей, например, Hoecker Polytechnik (Австрия), C. F. Nielsen (Дания), Schuko (Германия), СO.MA.FER, Mischi Maschinen (обе - Италия), схожи с представленными в таблице 4: максимальное давление прессования - свыше 150 МПа, достаточно для производства брикетов высокой плотности - более 1,2 г/см3.
В таблице 5 представлены сведения, дающие представление о рентабельности производства биотоплива с использованием гидравлического пресса.
Качество получаемого брикета зависит от многих факторов, основные: химический состав и физическое состояние прессуемого материала, его влажность, фракционный состав и размер брикетируемых частиц, температура нагрева перед прессованием, усилие прессования, продолжительность выдержки под давлением.
Прочность брикетов с включением коры и брикетов, изготовленных только из коры, ниже прочности брикетов из опилок без включения коры. При давлении прессования 100 МПа прочность на изгиб брикетов из опилок составляет около 3,5 МПа, брикетов из коры - 1,75 МПа. Прочность корьевых брикетов приблизительно вдвое ниже прочности брикетов из опилок.
На рис. 3 представлен график, иллюстрирующий влияние влажности опилок на прочность получаемых брикетов. Наилучшие показатели достигаются при прессовании опилок влажностью 5-10%.
При влажности материала менее 5% прочность брикетов снижается. Затруднительно однозначно определить, чем обусловлено снижение прочности: пониженной плотностью брикетов из более жестких сухих опилок либо структурой брикетов.
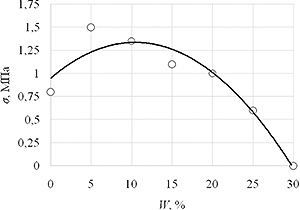
Рис. 3. Влияние влажности опилок на прочность брикетов