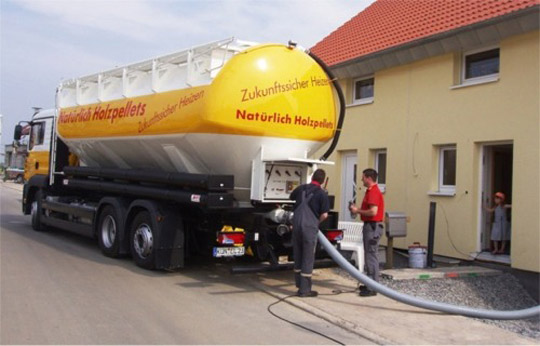
Пневморазгрузчик представляет собой цилиндрическую или прямоугольную емкость, разделенную на несколько камер (отсеков) с компрессором для подачи воздуха, установленную на шасси грузового автомобиля, либо в виде прицепа или полуприцепа к седельному тягачу. Эти машины могут перевозить от 15 до 28 т пеллет, а с дополнительным прицепом еще больше. Посмотрим на примере, как происходит загрузка и выгрузка одной из таких машин.
После получения маршрутного листа водителем автотранспорт ставится под загрузку пеллет. Автосилос состоит из четырех камер, в каждую из которых загружается 4,75 т пеллет. Перед загрузкой водитель набирает на пульте, расположенном на консоли склада, специальный ID-код. Пеллеты подаются из склада наверх наклонным ленточным транспортером, в конце которого расположено сито (через него древесная пыль отсеивается и сбрасывается в желоб транспортера - таким образом содержание пыли в пеллетах минимизируется до 1%), а над приемным люком автосилоса пеллеты ссыпаются в синтетический рукав большого диаметра и из него поступают в емкости транспорта.
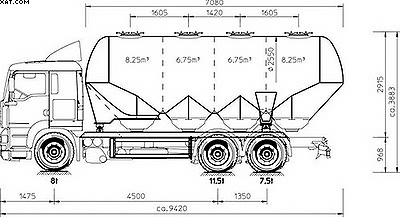
Каждый пеллетный склад, как правило, оборудован двумя штуцерами-патрубками: один для закачки пеллет, другой для отсасывания пыли и снятия избытка давления на складе. Для идентификации их окрашивают в разный цвет. По прибытии автосилоса к заказчику водитель подключает одну из камер к приемному штуцеру пеллетного склада, для чего используется резиновый 3-дюймовый (на новых моделях 4-дюймовый) шланг длиной 6 м с внутренним тефлоновым покрытием для уменьшения истираемости гранул). Если расстояние от транспорта до склада больше 6 м, есть возможность соединить несколько шлангов (максимум до 25 м). Затем подключается второй шланг - для параллельной откачки воздуха с пылью из склада.
Во время закачки пеллет пыль отсасывается в отдельный мешок - так же, как это делается обыкновенным пылесосом, работающим от компрессора. Затем водитель-оператор включает из кабины компрессор, берет ручной дистанционный пульт управления, подходит к задней части силоса, открывает первую камеру-отсек, и, как говорится, процесс пошел. Пеллеты вдуваются по шлангу в пеллетный склад. Для правильного распределения нагрузки и лучшей управляемости автосилоса при переезде к следующему месту выгрузки сначала освобождается первая камера силоса (считая от кабины). После первой выгружается четвертая, а затем вторая и третья камеры. А в зимнее время при скользкой дороге четвертый отсек никогда не выгружается полностью, чтобы немного подгрузить задние оси автомобиля.

После окончания выгрузки водитель распечатывает в кабине с помощью бортового компьютера накладную и счет и дает их на подпись получателю. Одновременно все данные (сколько и где выгружено пеллет, накладные, счета) посредством GPS поступают в центральный офис. В Германии весь цикл - погрузка-доставка заказчикам и выгрузка - занимает, как правило, один рабочий день. Сеть производителей пеллет и трейдеров каждый год расширяется, поэтому радиус доставки пеллет автопневмотранспортом - максимум 150 км от склада загрузки.
В обязанности водителя-оператора входит также функция проверки склада перед выгрузкой в него пеллет. Он обязан выяснить, заземлены ли приемные патрубки и штуцеры, правильно ли установлены специальные отбойные листы для предотвращения разрушения гранул при ударах о стенки склада, был ли остановлен за несколько часов до начала заполнения склада пеллетный котел (в противном случае тлеющие гранулы или искры могут во время работы компрессора попасть в пеллетный склад и привести к его возгоранию) и т. п. Опытный водитель-оператор, кинув лишь один взгляд на топливный склад, уже знает, под каким давлением лучше закачивать в него пеллеты.
Первые специализированные автомобили для перевозки пеллет не были оборудованы дистанционными пультами управления и контроля, водитель стоял в кормовой части машины у рычагов и переключателей, и от него требовалось четко уловить момент, когда склад уже наполнен или в камере заканчиваются пеллеты и необходимо выключить компрессор. Затем на автосилосах стали устанавливать датчики, которые включением лампочки на панели управления сигнализировали о том, что в камере осталось 200 кг пеллет. Когда над приемным мешком пылесоса появлялось облачко пыли, это означало, что склад заполнен и пылесос откачивает пеллеты назад из склада, поэтому требовалось срочно выключить компрессор. Сегодня все индикаторы сенсоров выведены на дистанционный пульт и управление процессом выгрузки максимально упростилось. Однако профессионалы могут вполне обходиться без пульта. Недаром в Германии водителя-оператора автопневмотранспорта для перевозки пеллет называют Pellettankmann, что можно перевести как «специалист по заправке пеллетами» или просто «заправщик пеллетами» - по аналогии с заправщиком ГСМ.
Кстати, с октября 2010 года в ФРГ начала работать первая полностью автоматизированная заправочная пеллетная станция фирмы Westerwalder Holzpellets GmbH (производитель пеллет). Станция работает с 6 до 22 часов ежедневно независимо от часов работы офиса. Клиент подъезжает на своем автотранспорте под загрузочное устройство под силосом и загружает в свою емкость (цистерну, контейнер и т. п.) необходимое количество пеллет, которое в цифрах предварительно набирает на специальном дисплее. Оплата выполняется сразу после окончания загрузки - банковской картой через терминал. Все как на обычной АЗС. Такие автоматизированные станции для продаж пеллет насыпью начали строить и в других регионах Германии. Для клиентов это очень удобно: во-первых, приобретать пеллеты на такой станции дешевле, чем покупать их в магазине в мелкой расфасовке; во-вторых, можно купить небольшое количество, например, несколько сотен килограммов, в отличие от заказа с доставкой автосилосом, когда приходится оформлять минимальный объем 1-2 т.
При выгрузке пеллет из автосилосов от работы компрессора создается сильный шум, который мешает жителям домов, особенно если разгрузка выполнятся рано утром или поздно вечером. Поэтому в последние годы автосилосы были оборудованы малошумными компрессорами и снабжены дополнительной звукоизоляцией (обычно уровень шума при выгрузке составляет 95-110 дБ, а на новых машинах - до 75 дБ, то есть тише работающего двигателя).
Во многих европейских городах очень плотная застройка: узкие улочки, как правило, с односторонним движением, мосты автомобильных развязок и пешеходных переходов небольшой высоты. Все это создает проблемы с доставкой потребителям пеллет большегрузным автотранспортом. Зачастую владельцы пеллетных котлов, проживающие в городах, вынуждены приобретать пеллеты, расфасованные в биг-бэги или в 15-20-килограммовые мешки. В пересчете на тонну такая покупка обходится дороже, чем при доставке насыпью.
В июне 2011 года в федеральной земле Бранденбург впервые в Германии решили проблему доставки пеллет насыпью в городские кварталы с использованием малотоннажного пневмоавтотранспорта. Фирма Tyroller Hydraulik GmbH из г. Херцберг, расположенного в 100 км к югу от Берлина, специализируется на производстве гидравлических систем, а также на изготовлении специализированного автотранспорта. Идея расширения производства за счет запуска в серию небольших автосилосов для транспортировки пеллет возникла у руководства фирмы еще в 2009 году в связи с тем, что по соседству с компанией строился пеллетный завод, а основной рынок сбыта для пеллет в регионе - это Берлин с пригородами, где малотоннажный транспорт для доставки пеллет просто незаменим.
К проекту по созданию такой машины подключились еще несколько компаний: Kommunaltechnik Instandsetzung Fertigungstechnik GmbH (KIF), которая взялась за разработку кузова, PAARI Waagen und Anlagenbau GmbH & Co. KG, которая отвечала за бортовую электронную систему взвешивания, и Hans Engelke Energie OHG - трейдер, который занимается биотопливом. Консорциум, образованный этими компаниями, получил грант в сумме 150 тыс. евро (около 60% общей суммы инвестиций в этот проект) по федеральной инновационной программе Zentralen Innovationsprogramm Mittelstand (ZIM) в сфере развития автотранспорта. В рамках проекта одной из самых трудных была задача добиться максимально возможной грузоподъемности новой машины - 5,5 т (9 м3) при наименьшем собственном весе грузовика 6,49 т. Общий вес загруженной машины составил 12 т, что позволяет ездить по немецким автобанам без уплаты специальной дорожной пошлины на большегрузный автотранспорт. В конструкции использовано двухосное шасси MAN TGL 12.180. Вес грузовика удалось минимизировать за счет кузова, изготовленного из «сэндвич»-панелей из монопана (слоистый пластик из полипропилена). Внутри этих панелей проложены воздушные трубопроводы, которые являются дополнительно элементами жесткости кузова при его малом весе (всего 2 т).
В нижней части ваннообразного кузова (как у пеллетного склада) установлен ленточный транспортер - он сдвигает пеллеты при выгрузке к кормовой части кузова, где расположен лопастный шлюз, из которого за счет работы компрессора пеллеты вдуваются в разгрузочный шланг. Благодаря такой конструкции воздух, подаваемый компрессором, минует транспортную емкость кузова, поэтому для пневматической выгрузки пеллет требуется меньшее давление, чем при выгрузке из классических автосилосов.
По сравнению с крупногабаритными собратьями, у компрессора нового автосилоса меньше мощность, размеры и вес, но зато работает он намного тише, да и производительность выгрузки пеллет новой системы больше. Скорость выгрузки пеллет в среднем 1 м3 (650 кг) за 7 минут. Разработчикам удалось достигнуть возможности выгрузки пеллет при общей длине разгрузочных шлангов до 60 м. Высота грузовика с кузовом - 2,61 м (без загрузки) и 2,53 м (с загрузкой), ширина - 2,30 м, длина - 6,77 м. Для сравнения: 18-тонный автосилос высотой 3,84 м, а шириной 2,55 м. Стоимость новой машины - 130 тыс. евро. Сейчас компания Tyroller Hydraulik GmbH разрабатывает подобные облегченные кузовы разных типоразмеров для разных шасси. В Европе новый 18-тонный автосилос перевозит в среднем 3 тыс. т пеллет в год и окупается примерно за четыре года.
Сегодня в Германии и других европейских странах уже сформировался рынок бывших в употреблении специализированных автомобилей для перевозки пеллет, на котором этот транспорт можно приобрести по вполне приемлемым ценам и в хорошем техническом состоянии. Наиболее экономически целесообразным вариантом можно считать приобретение полуприцепа.
Для Украины использование автопневмотранспорта для доставки пеллет - довольно перспективный бизнес. Сегодня главная проблема - это, по сути, полное отсутствие специально оборудованных складов для хранения пеллет. Но, скорее всего, если производитель пеллет или трейдер предоставит своим заказчикам возможность такой доставки, то потребитель будет одновременно с установкой пеллетного котла оборудовать и пеллетный склад. А тем, у кого уже установлен котел, не составит большого труда и больших затрат переоборудовать место для хранения пеллет.