Производство пеллет и брикетов
В последнее время появился огромный интерес к производству твердого биотоплива в связи с резким подорожанием газа и возможным сокращением подачи его потребителям.
Существует несколько методов переработки биомассы для получения пеллет и брикетов. Я хочу поделиться своим накопленным опытом в производстве твердого биотоплива. На первом этапе необходимо не ошибиться с выбором технологии переработки отходов биомассы.
Различают несколько технологий производства пеллет и брикетов. Чем отличаются пеллеты от брикетов – это форма и размеры. Пеллеты, как правило, имеют цилиндрическую форму диаметром от 3мм до 8мм и длиной от 5мм до 40мм. Брикеты же могут иметь цилиндрическую, прямоугольную, овальную и другие формы, а размеры обычно составляют: диаметр от 20мм до 100мм и длина до 300мм. Я говорю о самых распространенных размерах и формах.
Итак пеллеты (гранулы)
Пеллеты производят на грануляторах. Существует два основных вида грануляторов – с плоской и круглой матрицей.
Плоская матрица представляет собой плоский металлический диск из высококачественной стали диаметром от 100мм до 1250мм и толщиной от 20мм до 100мм. Сталь, из которой изготавливается матрица, должна иметь свойства повышенной износостойкости и возможностью закалки в пределах 60 единиц по шкале твердости Роквелла. Обычно это отечественная сталь 40Х, шведская HARDOX 500, сталь 20CRMN или другой марки.
Производительность гранулятора зависит от диаметра матрицы. Грануляторы с матрицей диаметром 1250мм могут выдавать до 3 тонн пеллет в час. Лидером в производстве таких грануляторов является немецкая фирма KAHL. Стоимость такого гранулятора и периферийного оборудования к нему очень и очень высокая. Я знаю несколько украинских фирм, которые потратили от 3 до 10 млн Евро на заводы с подобным оборудованием, но положительных результатов за 3-4 года почти нет. Производство пеллет – это очень сложное искусство. На таком оборудовании нужна высокая культура производства.
Второй вид – грануляторы с круглой матрицей с диаметром до 550мм. Матрица, как правило, выполняется из нержавеющей износостойкой стали, которая калится до твердости 45-50 кгс по Роквеллу. Производительность таких грануляторов может достигать 3т/час.
Вообще, когда мы говорим о производительности, мы должны дифференцировать ее величину от качества самого сырья, от его состава при идеальной подготовке сырья перед подачей в гранулятор. Еще на производительность существенно влияет установленная мощность электродвигателя. Брендовые фирмы, выпускающие грануляторы, устанавливают редуктор с параметрами крутящего момента и передаточным числом с высоким КПД, позволяющим использовать электродвигатель с оптимальной мощностью.
Небольшие украинские предприятия, как правило, устанавливают на гранулятор редуктор заднего моста грузового автомобиля. На 90% китайских грануляторов установлен такой редуктор. Это работает, но требует на 10-15% больше энергозатрат.
Грануляторы с круглой матрицей очень давно применяются на территории СНГ для производства комбикорма. Это грануляторы серии ДГ и ОГМ. Наши умельцы переделывают их под производство топливных пеллет. Собственно необходимо изготовить новую матрицу под нужное сырье и вкатывающие ролики. Принцип работы однотипных грануляторов подобен.
Существует третий тип грануляторов мало распространенный в СНГ - это гибрид гранулятора с плоской и круглой матрицей.
Круглая матрица располагается формирующими каналами параллельно основанию, а вкатывающие ролики закатывают сырье, поступающее в рабочие органы гранулятора, под собственным весом. Такая модель сегодня очень популярна в Китае.
Периферийное оборудование
Новички, начинающие производство пеллет, как правило, не понимают, что гранулятор – это 20% успеха производства пеллет. Дробление, сушка, тонкое измельчение, водоподготовка, смешивание и дозирование – вот те процессы, без которых ни один гранулятор не будет работать стабильно. Сырье, которое будет гранулироваться, необходимо особо тщательно подбирать. По порядку.60% желающих наладить бизнес гранулирования хотят перерабатывать древесину. Крупные куски древесины необходимо измельчить до размера щепы не более 50мм. Это достигается в зависимости от размеров различными машинами:
1. Горизонтальный щепорез (стационарный/мобильный)
2. Барабанная дробилка (стационарная/мобильная)
3. Шредер (стационарный)
Это оборудование существенно отличается друг от друга по цене и производительности.
Щепу нужно просушить до содержания влаги ≤10%. Это очень непростой процесс. Стоит понимать, что необходимо связанную влагу под воздействием температуры выделить из сырья в виде пара, а затем вентилятором удалить из сушильного устройства.
Первое, что следует знать, и это есть основа процесса сушки, сырье до входа в сушку должно быть с влагой ≤45%. При содержании более высокого показателя в сушке образуется избыточный пар, и процесс испарения замедляется до нуля.
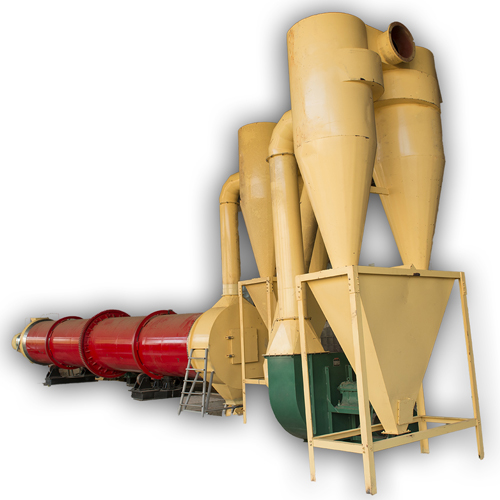
Для каждого вида сырья есть предел температуры горячих газов на входе в сушилку. Так, например, у пшеничной соломы процесс пиролиза начинается при t≈ 200 градусов C, а у древесины t≈ 400 градусов C. После интенсивного процесса пиролиза сырье теряет свойство «вязаться», а значит, гранула рассыпается.
Чем меньше мы оставим влаги в сырье (≤10%), тем производительней будет работать молотковая дробилка, которая должна дать фракцию равную 1/2 диаметра канала матрицы. Так, если мы делаем пеллету диаметром 6мм, то фракция должна быть ≤3мм.
После молотковой дробилки необходимо подготовить сырье в смесителе-дозаторе. Здесь надо увлажнить сырье приблизительно до 14% в зависимости от конструкции гранулятора, качества сырья и уровень влаги подбирается экспериментально. Сырье в гранулятор подается дозировано.
Параметры, влияющие на работу гранулятора:
1. Глубина формирующих каналов матрицы подбирается для каждого сырья индивидуально. Длина канала влияет на плотность гранулы.
2. Фаска на входном канале матрицы (зенькование) подбирается под каждое сырье.
3. Форма и диаметр вкатывающих роликов подбирается по сырью.
4. Обороты главного вала гранулятора, как правило, лежат в пределах 80-120 об/мин или скорость роликов должна быть 2,2-2,7 м/секунду.
5. Конструкция устройства не позволяющая подниматься легкому сырью от плоскости матрицы (для грануляторов с плоской матрицей).
6. Мощность двигателя влияет на производительность гранулятора. Чем жестче сырье, тем мощнее нужен электродвигатель.
Сырье для гранулирования
Зачастую звонят люди, начинающие бизнес гранулирования, по поводу гранулятора. На вопрос о том, какое сырье они собираются гранулировать, мне отвечают, что есть часть древесных отходов, солома, некормовые отходы с/х и т.д. Т.е. существует некомпетентное мнение, что в гранулятор можно бросать, что угодно и получать гранулу. Скажу сразу – 95% желающих производить миксированную гранулу потерпит фиаско от такой затеи.
Мои коллеги из Умани уже много лет занимаются гранулированием соломы. Они мне рассказали, что солома одно и того же сорта пшеницы с разных полей гранулируется по-разному. Бывает так, что с определенного поля и вовсе не гранулируется.
Гранулы (пеллеты) производят двух видов: для промышленного использования и бытовые по европейским стандартам.
Первые используются в промышленных печах и топках. Зачастую их измельчают в пыль перед использованием, а затем подают в пылевые топки. Так делают на польских ТЕЦ.
Бытовые гранулы дороже в производстве, но пользуются спросом в Европе. Изготавливаются пеллеты диаметром 6мм из хвойных пород древесины с предварительной очисткой от коры.
Хочу предложить несколько групп сырья для гранулирования:
Легко пеллетируемые
1. Сено люцерны
2. Смеси зерновых
Пеллетируемые
1. Древесина хвойных пород
2. Отходы коробочки сои
3. Отходы чечевицы
4. Шелуха подсолнуха
5. Солома сои
Плохо пеллетируемые
1. Смешанные отходы с/х
2. Лиственные породы древесины
3. Лигнин
4. Торф
5. Смеси биомасс
Нерекомендуемые
1. Шелуха риса (высокая абразивность, низкая теплотворность, высокая зольность)
2. Древесина фруктовых деревьев, виноградная лоза (высокая абразивность, требует высокой прочности оборудования, спекаемость при сгорании).
Зачастую хотят перерабатывать то, что видят, например, камыш. Обычно я предлагаю убрать 0,5га плантации камыша, взвесить его, посчитать себестоимость уборки, и уже не захочется его гранулировать.
Мы должны понимать к чему мы стремимся. Наша конечная цель – это продать наш продукт и получить прибыль. Прежде чем начать этот бизнес необходимо знать, сколько и какое сырье вы сможете использовать, кому и какое количество вы сможете продать. После анализа подобрать оборудование и составить бизнес-план.
Еще раз скажу, что гранулирование биотопливных гранул очень сложный процесс. Прежде чем вы начнете этим заниматься, ответственно подойдите к этому вопросу, все просчитайте.
Брикетирование
На мой взгляд, брикетирование более простой способ получения биотоплива. Брикет – это продукт замещения угля, и в данное время он очень востребован на внутреннем рынке Украины.
Существует 5 основных способов производства брикетов:
1. Ударно-механический – Нильсен (Nielsen)
2. Экструзионный с температурным нагревом – ПиниКей (Pini&Kay)
3. Гидравлический типа РУФ (RUF)
4. Кольцевой
5. Экструзионный холодный способ.
Одним из распространненых способов производства брикетов является ударно-механический. Принцип работы – кривошипно-шатунный механизм приводит в движение поршень, который с большой частотой бьет по сырью, подаваемое в выходную головку шнековым дозатором. Выходная головка имеет такую форму, что позволяет формировать брикет нужной цилиндрической формы. На выходе брикет подпирается либо гидравлическим способом, либо механическим. В большинстве случаев участок линии движения брикета от головки до участка складирования составляет более 10 метров.
Лидером среди станков для производства таких брикетов является датская фирма C.F.Nielsen, чье оборудование может достигать мощности до 1,5т/час. Технология требует очень хорошую подготовку сырья (влага, фракция, однородность) и желательно окоркованные хвойные породы древесины. Оборудование данной компании очень дорогое – около 500.000USD. Такой тип прессования широко используется в Индии и оборудование этой страны имеет неплохое качество.
Брикетер экструзионный Pini&Kay с нагревом распространен в Украине благодаря низкой стоимости от 2000USD до 4000USD. Брикет получается очень красивый и плотный с отверстием внутри. Но на этом заканчиваются все плюсы данного метода производства.
Для получения брикета сырье должно быть высушено до показателя влаги меньше 8%, что весьма проблематично. Недостатком технологии является необходимость измельчения сырья до мелкой фракции, а также очень низкая производительность - от 50кг/ч до 200кг/ч. Через каждые 6-8 часов работы необходимо наваривать шнек экструдера износостойкими сплавами. В результате выходит очень высокая себестоимость брикета.
Брикет типа РУФ производят на гидравлических прессах немецкой фирмы RUF, латвийской RMP и польской BIZON. Давление в таких станках создается до значения 300 бар. Для производительности 400 кг/ч необходимо формировать брикет 15х6х11мм. Такой продукт на рынке Украины не имеет массового спроса из-за большого размера. Кроме того влага сырья должна быть меньше 14%, а фракция меньше 3мм. Хотя эти пресса самые надежные из всех видов данного оборудования для производства брикетов, но очень дорогие – от 48000€ до 100000€.
Еще одним видом гидравлических прессов является так называемые пресса Nestro, которые выпускает немецкая фирма Nestro Lufttechnik GmbH. Они отличаются от прессов типа RUF тем, что противодействующей силой главного цилиндра есть выходная головка с гидравлическим замком. Такие показатели как низкая производительность – в среднем 100кг/час, высокие требования к подготовке сырья и высокая стоимость сделали этот пресс нераспространенным на территории Украины, хотя брикеты после этого пресса имеют довольно приятный товарный вид.
Кольцевой брикетер на 45 матриц с установленной мощностью 60кВт имеет производительность до 3т/час. Данный высокоэффективный брикетер хорошо работает на сельскохозяйственных отходах и минимальные требования к сырью это содержание влаги от 22% до 30%, а фракция по соломе до 60мм.
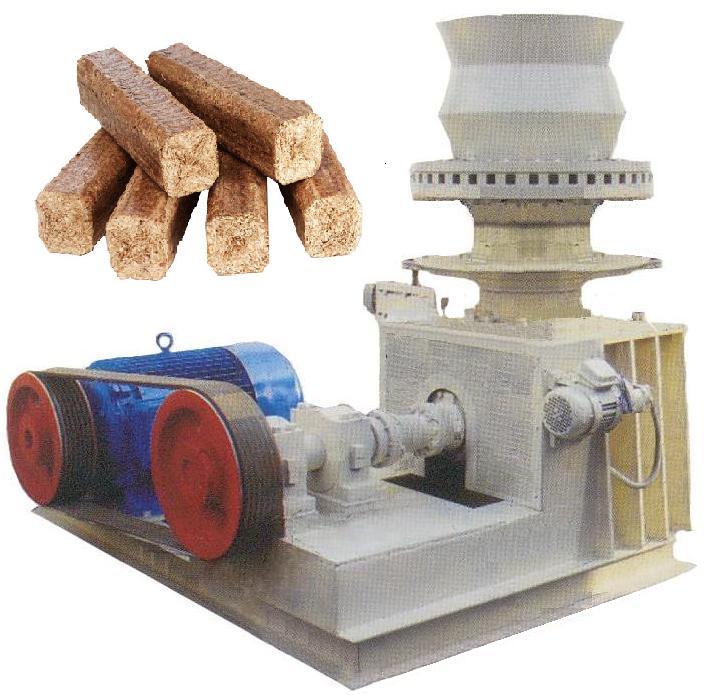
Такой брикетер работает в производственном цехе компании «Зерма-Украина» Херсонской области на соевой соломе. Готовый брикет имеет размеры в сечении 32х32мм. В Украине подобных брикетеров нет. Оборудование стоит относительно недорого – 32000USD, а срок окупаемости составляет 5 месяцев.
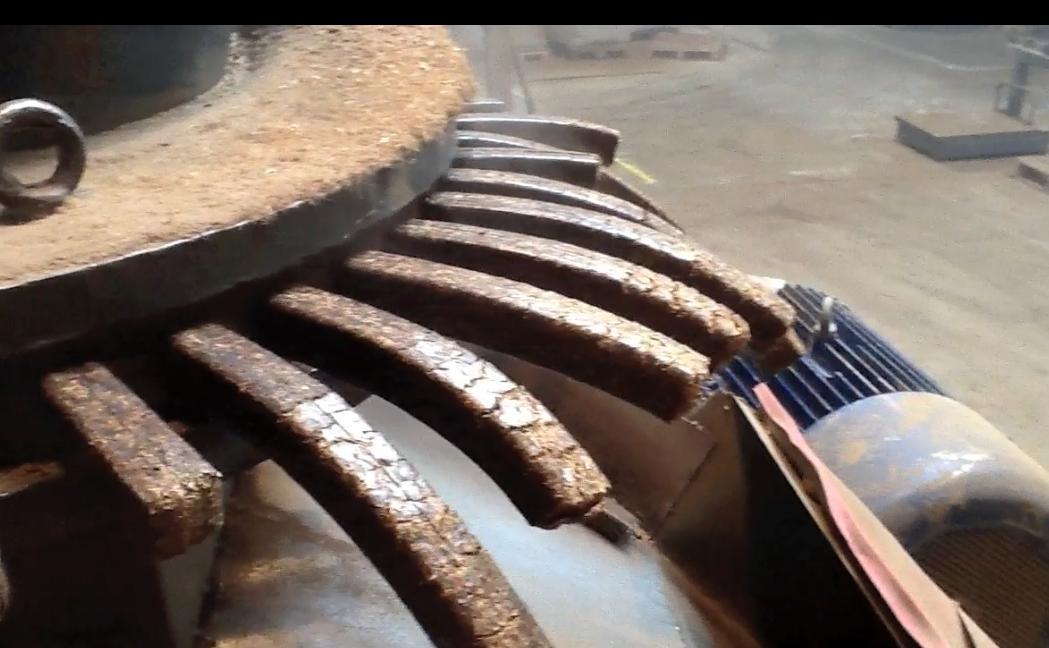
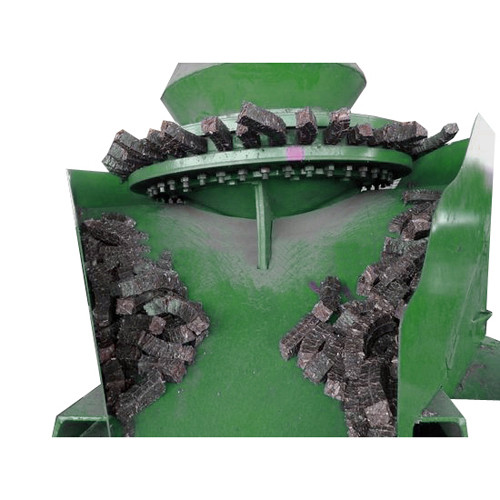
Брикетер холодной экструзии – данное оборудование хорошо подходит для экструдирования торфа, угольной пыли, соломы сои, жирных отходов подсолнуха. Производительность от 1т/ч до 2,5т/ч. На производственной площадке «Зерма-Украина» экструдер производит брикеты диаметром 32мм с высокой теплотворностью из отходов подсолнуха и соломы сои.
Положительными факторами являются низкая установочная мощность 32кВт, нет необходимости сушить сырье, высокая производительность и невысокие трудозатраты. А отрицательным фактором является необходимость додрабливать солому через сито с диаметром ячейки 8-10мм.
Когда я вам описывал оборудование, я всегда говорил о влаге и фракции. Помните, что периферийное оборудование также важно, как и гранулятор и брикетер.
Генеральный директор ООО «Зерма-Украина»
Гребенюк Петр Алексеевич
М.т.: +38 050 418-52-02
Тел.: +38 05536 21402
www.tmgreenbull.com.ua
Гребенюк Петр Алексеевич
М.т.: +38 050 418-52-02
Тел.: +38 05536 21402
www.tmgreenbull.com.ua