Технологічні процеси брикетування можуть включати наступні основні операції: транспортування сировини до брикетуючі установці; подрібнення великих деревних відходів; сепарацію (сортування сировини за розмірами фракцій); сушку; термообробку; пресування (формування брикету); зберігання і транспортування до місця споживання. Слід зазначити, що перераховані операції виконуються не у всіх технологічних процесах брикетування.
До паливним брикетам пред'являються певні вимоги, регламентовані стандартами. У табл. 1 представлені технічні вимоги до паливних брикетів, розроблені в Росії.
В каждой стране действуют свои стандарты, регламентирующие требования к твердому биотопливу, например, в США - Standard Regulations & Standards for Pellets in the US: The PFI; в Великобритании - The British BioGen Code of Practice for biofuel; в Швейцарии - SN 166000; в Швеции - SS 187120; в Австрии - ONORM M 7135; в Германии - DIN 51731 и DIN plus.
В 2011 году в Европейском союзе введены стандарты качества биотоплива EN 14961-2 (табл. 2).
Резюмируя данные, представленные в таблице 2, отметим, что плотность топливных брикетов должна быть выше 1 г/см3, влажность - не превышать 15%, а зольность составлять 0,7-3%; в брикетах допускается содержание коры.
Оценим низшую теплоту сгорания брикетов по формуле Д. И. Менделеева:
Таблиця 1. Технічні вимоги до паливних брикетів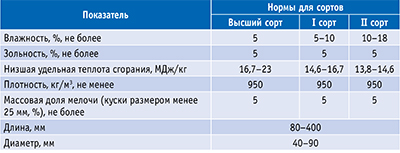
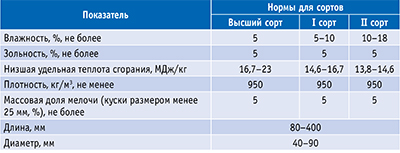
Таблиця 2. Вимоги до паливних брикетів за стандартом EN 14961-2
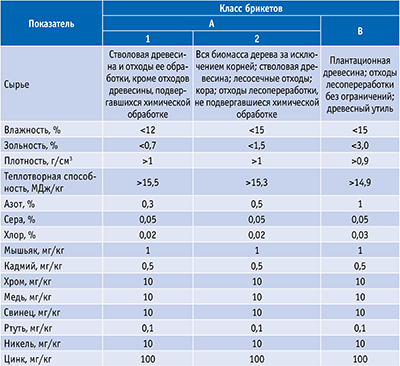
Де С - процентний вміст вуглецю в корі за масою, H - процентний вміст водню, O - процентний вміст кисню, W - відносна вологість матеріалу брикету.
За формулою (1) при C = 42%, H = 8%, O = 50% побудуємо графік, представлений на рис. 1.
Отже, при вологості нижче 15% вимога до мінімальної теплотворної здатності брикетів виконується автоматично.
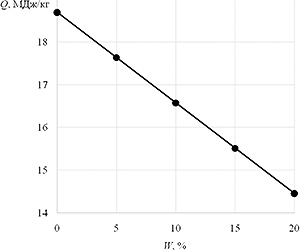
Сучасне пресове обладнання для брикетування
Основним обладнанням, що визначає продуктивність ділянки по виробництву брикетів, є преси. Відомі преси для брикетування деревних відходів наступних конструкцій: штемпельні з відкритою матрицею; копрові; шнекові; гідравлічні; ротаційні; ударно-механічні. Копрові і ротаційні преси широкого поширення не отримали.
Гідравлічні преси вважаються найбільш надійними і безпечними для обладнання сучасних високопродуктивних брикетних станцій.
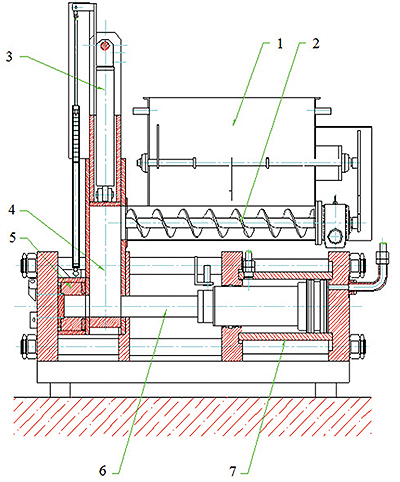
Рис. 2. Схема гідравлічного преса: 1 - бункер, 2 - завантажувальний шнек, 3 - поршень наповнювача, 4 - камера наповнювача, 5 - прес-форма, 6 - головний пресує поршень, 7 - пресує циліндр
Таблиця 3. Переваги та недоліки різних конструкцій пресів
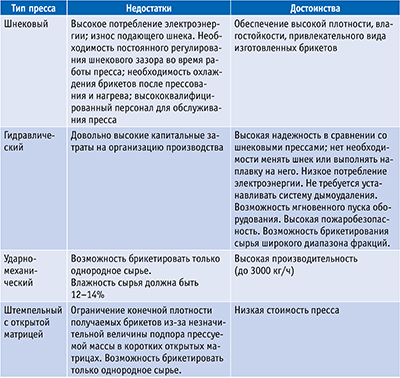
Таблиця 4. Технічні характеристики модельного ряду пресів фірми RUF (Німеччина) Технічні дані RUF 100 RUF 200 RUF 400 RUF 600 RUF 1100
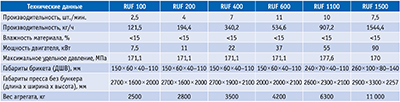
Таблиця 5. Орієнтовна оцінка рентабельності продукції брикетного виробництва
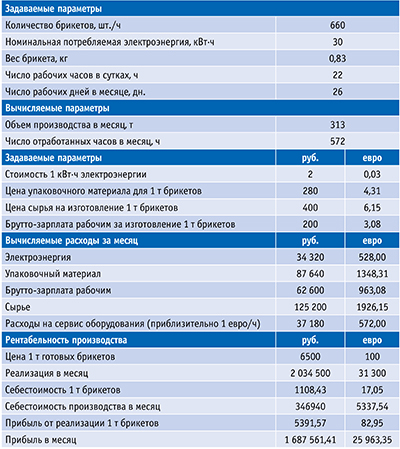
Операція брикетування на гідравлічних пресах здійснюється наступним чином (див. Схему гідравлічного преса на рис. 2).
Завантажувальний шнек подає матеріал, що знаходиться в бункері, в наповнювач, тривалість роботи завантажувального шнека пов'язана з системою автоматичного дозування матеріалу.
Після закінчення завантаження наповнювача і зупинки завантажувального шнека поршень наповнювача виконує попереднє стиснення матеріалу, що знаходиться в камері наповнювача. Головний пресує поршень пересуває попередньо стиснений матеріал в одну з двох камер прес-форми і стискає матеріал в щільний брикет.
Протягом цього етапу виштовхувачі, встановлені паралельно головному циліндру, виштовхують готовий брикет з другої камери прес-форми через спеціальні отвори в передній панелі. Поршень наповнювача піднімається вгору. Завантажувальний шнек починає подачу наступної порції пресованого матеріалу. Пресує циліндр повертається у вихідне положення, прес-форма переміщається, після чого операції повторюються.
Характеристики пресів інших виробників, наприклад, Hoecker Polytechnik (Австрія), CF Nielsen (Данія), Schuko (Німеччина), СO.MA.FER, Mischi Maschinen (обидві - Італія), схожі з представленими в таблиці 4: максимальний тиск пресування - понад 150 МПа, досить для виробництва брикетів високої щільності - більше 1,2 г / см3.
У таблиці 5 представлені відомості, що дають уявлення про рентабельність виробництва біопалива з використанням гідравлічного преса.
Якість одержуваного брикету залежить від багатьох факторів, основні: хімічний склад і фізичний стан пресованого матеріалу, його вологість, фракційний склад і розмір брікетіруемих частинок, температура нагріву перед пресуванням, зусилля пресування, тривалість витримки під тиском.
Міцність брикетів з включенням кори і брикетів, виготовлених тільки з кори, нижче міцності брикетів з тирси без включення кори. При тиску пресування 100 МПа міцність на вигин брикетів з тирси становить близько 3,5 МПа, брикетів з кори - 1,75 МПа. Міцність корьевих брикетів приблизно вдвічі нижче міцності брикетів з тирси.
На рис. 3 представлений графік, який ілюструє вплив вологості тирси на міцність одержуваних брикетів. Найкращі показники досягаються при пресуванні тирси вологістю 5-10%.
При вологості матеріалу менше 5% міцність брикетів знижується. Скрутно однозначно визначити, чим це зумовлено зниження міцності: зниженою щільністю брикетів з більш жорстких сухих тирси або структурою брикетів.
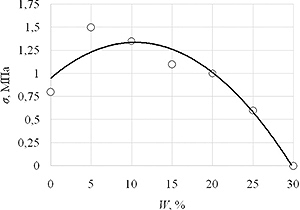
Рис. 3. Вплив вологості тирси на міцність брикетів