Экспорт древесных пеллет может стать привлекательным направлением для инвестиций.
Вместе с ростом потребления этой продукции в Европе, растет и предложение нового оборудования для производства гранул.
- Производительность гранулятора зависит от количества и диаметра отверстий матрицы, а также от ее площади.
- Электрическая мощность гранулятора в пересчете на 1 т выпускаемых пеллет должна составлять 70–100 кВт.
- На производство 1 т пеллет затрачивается 120–180 кВт/ч, из них 60–80 кВт/ч – на процесс гранулирования.
Модельный ряд основного оборудования для изготовления пеллет – грануляторов – как и перечень компаний-производителей, постоянно растет, совершенствуются их конструкции. На российском рынке свои разработки представляют как отечественные производители – ALB Group, «Невские Технологии – Инжиниринг», «Русский Гранулятор», так и иностранные. Компании Amandus Kahl GmbH & Co. KG (Германия) и California Pellet Mill Co (США/Нидерланды) производят прессы мощностью от 500 кг до 5 т гранул в час. Andritz Sprout A/S выпускает оборудование для гранулирования мощностью 3,5 т в час. Фирма Sweden Power Chippers AB (Швеция) представляет грануляторы малой производительности – от 150 до 450 кг/ч. Также грануляторы небольшой мощности, до 1 т в час, изготавливает Радвилишкский машиностроительный завод (Литва). Немецкий производитель Muеnch-Edelstahl GmbH выпускает грануляторы мощность от 500 кг до 2 т в час. Компания AVS Slovakia, s.r.o. (Словакия) поставляет грануляторы для древесины двух типоразмеров – мощностью 2 т в час и 5 т в час.
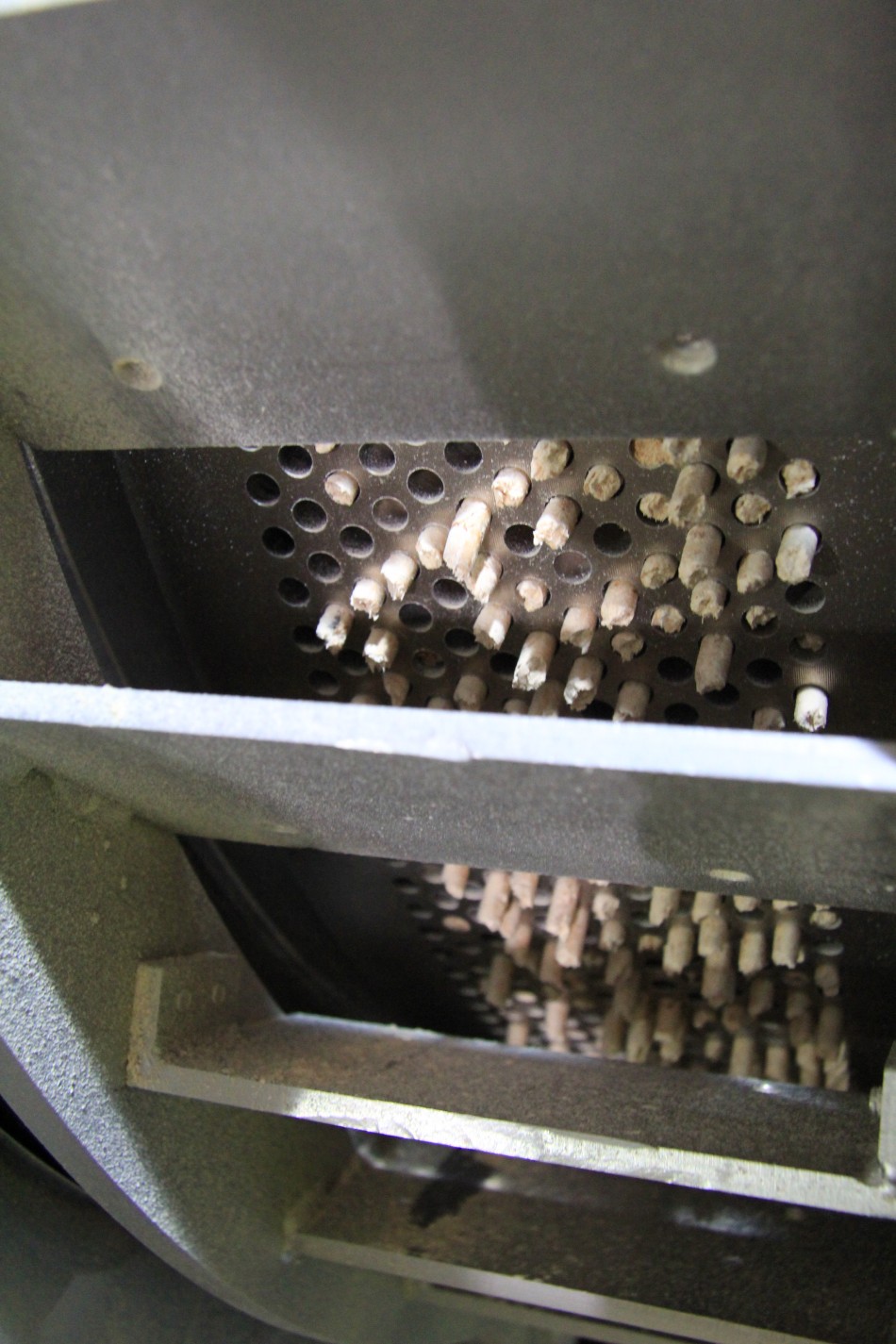
Также производят прессы, но не поставляют их в Россию или только начинают выходить на этот рынок, компании: Salzhausener Maschinenbautechnik SALMATEC GmbH (Германия), LA MECCANICA s.r.l. (Италия), M•B•Z Mühlen (Германия), TRITEC GmbH (Германия), Akademia2003 (Италия), Van Aarsen International Headquarters (Нидерланды), STOZA s.r.o. (Чехия), Gama Pardubice s.r.o. (Чехия), ZE.PI. SRL (Италия), General Dies S.r.l. (Италия), Bliss Industries, Inc. (США), «Грантех» (Украина), Zhengchang Group Co., Ltd. (Китай), Bühler AG (Швейцария).
Типы грануляторов
По конструкции прессы-грануляторы могут быть с плоской матрицей, с круглой матрицей, с двумя вертикальными вращающимися матрицами, гибрид гранулятора с плоской и круглой матрицей. В грануляторах с плоской горизонтальной вращающейся матрицей через отверстия в ней материал продавливается прессующими вальцами и формируется в гранулы. Основными элементами пресса являются ролики, закрепленные на приводном валу, и плоская матрица. Такие грануляторы небольшие по размеру, имеют простую конструкцию, а потому подходят предприятиям с малым объемом переработки, а также частным хозяйствам. К недостаткам этого оборудования можно отнести то, что при определенной окружной скорости возникает относ материала под действием центробежных сил к периферии матрицы и, как следствие, неравномерная нагрузка на ее рабочую поверхность. Из-за разности угловых скоростей роликов происходит неравномерный износ поверхности матрицы и роликов. Очень сложно добиться одинакового зазора между всеми роликами и матрицей. При выходе из строя одного подшипника в ролике, как правило, меняются все подшипники на роликовой головке. Ремонт гранулятора с плоской матрицей обойдется дороже, чем гранулятора с круглой матрицей.
В грануляторах с круглой вертикальной вращающейся матрицей материал продавливается через отверстия матрицы прессующими вальцами и формируется в гранулы. В данной конструкции пресса каждый ролик индивидуально подводится к матрице, обеспечивая необходимый зазор и тем самым наилучшее качество получаемого продукта, а также равномерный износ роликов и матрицы. Прессы этой конструкции наиболее распространены, на их долю приходится около 90% всего рынка грануляторов. Их недостатком является большая окружная скорость и, как следствие, чувствительность к влажности и фракции гранулируемого материала, а также большее энергопотребление.
Грануляторы с двумя вертикальными, вращающимися в противоположных направлениях матрицами роликов не имеют. Матрицы расположены так, что их внешние диаметры накладываются друг на друга, как зубчатая передача. Такие грануляторы не нашли широкого применения из-за высоких эксплуатационных издержек и сложностей в работе. Гибрид гранулятора с плоской и круглой матрицей появился на рынке сравнительно недавно. Такой пресс-гранулятор 3000-200-10 представлен в России компаниями «ЛесИнТех» и Dieffenbacher (Германия). Оборудование сочетает в себе достоинства прессов с плоской и с кольцевой матрицей, при этом исключая такие их недостатки, как неравномерность износа матриц и роликов, долгое время их замены, отсутствие визуального контроля за процессом гранулирования. Гранулятор разработан для заводов большой производительности. Данная модель состоит из десяти узлов. Прессующий узел включает питатель, прессующий ролик и общую плоскую матрицу с заданным диаметром отверстий.
Грануляторы с шестеренчатым приводом самые дешевые в эксплуатации. В них нет больших потерь на трение, как в ременной передаче или в червячной паре. У них самая низкая стоимость и расход смазочных материалов. КПД одноступенчатой шестеренчатой передачи составляет 98%, клиноременной – 96% и уменьшается в процессе работы (износа ремней), КПД червячной передачи составляет 90%.
Грануляторы с клиноременной и с шестеренчатой передачами одинаково распространены. Достоинства клиноременной передачи – большая устойчивость к вибрациям и перегрузкам камеры гранулирования, которые поглощаются за счет ремней и валов. У грануляторов с шестеренчатой передачей нагрузки больше передаются на электродвигатель. Чтобы оборудование хорошо работало, ремни должны быть европейского производства, а это серьезно сказывается на его цене. При установке дешевых, менее качественных ремней шкивы поменяют профиль, и даже оригинальные ремни начнут быстро изнашиваться. Электроника грануляторов посредством датчиков следит за пробуксовыванием ремней, но на российских пеллетных предприятиях эти датчики быстро загрязняются из-за низкого уровня организации труда и слабой подготовки кадров. Срок службы клиноременной передачи составляет около 30 тыс. часов, но замена ремней стоит недорого. Срок службы шестеренчатой передачи составляет до 10 лет, но стоимость замены очень ощутима и может составить до 50% стоимости гранулятора. Два вышеперечисленных конструктивных признака являются принципиальными в классификации конструкций грануляторов.
Матрицы для пресса
Наиболее ответственной и изнашиваемой деталью гранулятора является матрица. Существует большое количество их разновидностей. Качественно изготовленная матрица должна сочетать в себе высокую сопротивляемость истиранию, поломкам и коррозии, обеспечивать высокую пропускную способность для достижения оптимальной производительности. Диаметр плоских матриц составляет 100–1250 мм, толщина – 20–100 мм. Диаметр круглой матрицы достигает 1000 мм.
Поскольку стоимость матриц высокая, на предприятиях уделяют большое внимание их сохранности и правильной эксплуатации. Матрицы изготовляют из разных материалов. Главные требования к материалам – высокая износоустойчивость и упругость. Хорошей износоустойчивостью обладают матрицы из нержавеющей стали. Как правило, используют сталь российского производства 40Х либо стали HARDOX 500 и 20CRMN. Используемая сталь должна быть износостойкой и иметь закалку 45–60 ед. по шкале твердости Роквелла.
По технологии изготовления различают упрочненные матрицы из нержавеющей стали, которые могут быть с вакуумной плавкой или со сквозной закалкой, а также науглероженные матрицы из легированной стали.
Получение гранул правильной формы при помощи непрерывного пропуска сырья через перфорированные матрицы в грануляторах достигается благодаря давлению валков и трению сырья о металлические стенки отверстий матриц. Чем длиннее эти отверстия, тем продолжительнее воздействие трения и тем прочнее получаются гранулы. Между диаметром гранул и длиной отверстий матрицы (длина прессования) существует соотношение, при котором получается установленная прочность гранул. Чем больше диаметр гранул, тем толще должна быть матрица. Живое сечение отверстий в матрице оказывает большое влияние на производительность гранулятора – чем оно меньше, тем меньше производительность. Часто в отверстиях матрицы делается зенковка, чтобы облегчить вход продукта в отверстия.
Толщина матрицы должна быть в 10 раз больше диаметра отверстий. При изготовлении матриц толщиной менее 50,8 мм применяют цековку отверстий, которая заключается в том, что сверлом рассверливают верхние кромки отверстий. Иногда делают фаски на отверстиях. Так, матрицы толщиной 50,8 мм могут иметь отверстия размером 4,8х38,1 мм с конусным углублением 12,7 мм. При этом эффективная длина образования гранул составляет 38,1 мм. Отверстия для прессования гранул диаметром от 2,4 до 4,8 мм имеют малую раззенковку у впуска. Отверстия для гранул диаметром 9,5 мм и выше не только раззенковывают, но и обрабатывают на конус до половины, а в некоторых случаях и больше.
По виду каналов различают матрицы с прямыми каналами, с раззенковкой на выходе, с конусным выходом, с пошаговым коническим выходом, с ключевым входом, с ключевым отверстием. При недостаточной толщине матрицы вышедшая из ее отверстия гранула сразу же разрушается. Раскалывание некоторых гранул по окружности свидетельствует о том, что продукт недостаточно сжимается или недостаточное время выдерживается в матрице под давлением. Производительность гранулятора зависит от диаметра отверстий матрицы, их количества, площади матрицы, а также качества шлифовки внутренней поверхности отверстий.
Наряду с матрицами на процесс прессования большое влияние оказывают и ролики. Их изготовляют из специальной закаленной стали. На поверхности роликов имеются рифления для уменьшения скольжения и для захвата гранулируемого материала. Когда поверхность роликов изнашивается от трения, возникающего при соприкосновении с сырьем и матрицей, ролики протачивают, вновь нарезают рифли или заменяют. Обычно заменяют матрицу и ролики одним комплектом. Как и у цепных пильных гарнитур (пары цепь – ведущая звездочка), изношенные ролики не ставят к новой матрице, и наоборот, так как поверхность изношенных роликов испортит поверхность новой матрицы. Матрица вместе с роликами составляет единый узел, они работают совместно и требуют правильной установки. Зазор между роликами и матрицей определяет степень сжатия. При нормальном расположении роликов от поверхности матрицы получаются гранулы требуемой прочности. Если зазор между роликами и матрицей увеличен, происходит предварительное сжатие слоя гранулируемого сырья, которое повышает давление в отверстиях матрицы, и гранулы получаются повышенной твердости. В таких случаях матрицы могут полностью забиваться продуктом, и тогда работа гранулятора останавливается.
Производство пеллет разделяется на два этапа: первый – образование предварительно сжатого слоя сырья; второй – продавливание сырья в отверстия матрицы и сжатие его благодаря трению в отверстиях. Если ролики касаются поверхности матрицы, то тогда предварительного сжатия сырья не произойдет, и из матрицы будут выходить мягкие гранулы или совсем неспрессованный продукт.
Более толстый слой предварительно сжатого сырья способствует образованию «смазки» между металлом ролика и матрицы, уменьшающей износ матрицы и валков. Слишком маленький зазор между роликами и матрицей дает тонкий твердый слой продукта, не обеспечивающий необходимой защиты от износа. В толстом слое сырья поглощаются тангенциальные силы, появляющиеся в результате движения ролика по матрице и стремящиеся загнуть острые концы ее отверстий, забивая или повреждая поверхность кусочками металла. Толстый слой сырья, предупреждающий преждевременный износ и поломку матрицы, следует применять для обеспечения безаварийной работы гранулятора.
Поскольку трение в отверстиях матрицы является важным фактором получения необходимого давления и твердости гранул, новая матрица с шероховатыми отверстиями, даже при тщательной ее обработке на заводе или при кратковременной приработке, дает очень твердые гранулы, а гранулятор показывает низкую производительность. Избыточное давление, создаваемое повышенным трением в отверстиях новой матрицы, можно компенсировать зазором между матрицей и роликами.
При выборе матрицы гранулятора прежде всего надо ориентироваться на вид планируемых к производству пеллет. Однако физико-механические свойства древесного сырья, напрямую влияющие на гранулирование и во многом на характеристики получаемых гранул, сильно варьируются в зависимости от породы древесины и условий места ее произрастания. Например, время выдерживания в матрице, зависящее от длины канала, влияет на качество гранул, особенно для хвойных пород. Затраты на энергию составляют значительную часть себестоимости гранул, поэтому матрицы грануляторов часто характеризуют таким показателем, как см2/кВт. В среднем на производство 1 т пеллет затрачивается 120–180 кВт/ч, из них 60–80 кВт/ч – на процесс гранулирования. Стоимость расходных материалов составляет около 100 руб. на 1 т, в зависимости от сорта древесины и содержания песка.
Большое влияние на энергоемкость процесса гранулирования, а также износ подшипников гранулятора оказывает эффективность системы смазки. Недавно на российском рынке появились грануляторы фирмы СРМ, на которых установлены ролики с масляной смазкой, в отличие от обычных – с консистентной смазкой. Система масляной смазки роликов (МСР) имеет ряд преимуществ, значительно продлевающих срок их службы. В системе МСР масло циркулирует по замкнутому контуру, обеспечивая непрерывную смазку роликов. Поток масла, идущий к каждому ролику, позволяет непрерывно контролировать температуру подшипников. Кроме этого, закрытая система предотвращает попадание в ролики абразивов, так как отфильтрованный поток масла удаляет частицы, приводящие к износу подшипников, а также значительно сокращает расход смазки. Система МСР позволяет снизить рабочую температуру подшипников роликов на 35 ºС (с 135 ºС до 100 ºС) и увеличить срок их службы на 7500 часов. Это приводит к годовой экономии более 900 тыс. руб. на гранулятор.
Выбор гранулятора
При выборе гранулятора следует обращать внимание на его электрическую мощность. В пересчете на 1 т выпускаемых пеллет эта цифра должна находиться в пределах 70–100 кВт. Как уже отмечалось, она зависит от конкретной породы древесины. Для одной и той же породы, но из разных регионов произрастания цифра тоже меняется. Еще один важный параметр – стоимость основных сменных элементов гранулятора: матриц и прессующих роликов. Кроме самой стоимости, выбирается соотношение стоимость/ресурс. Кроме того, имеют большое значение сроки и процедуры поставки запасных частей и расходных материалов.
Для небольших пеллетных цехов, чья производственная мощность не превышает 300 кг в час, лучше использовать грануляторы с плоской матрицей и простым охладителем. Рабочих экземпляров этого оборудования очень мало, и стабильно они работают только на мягкой и сухой хвое (лиственница). Сушилку опилок использовать экономически нецелесообразно.
Для предприятия производительностью от 500 кг до 1 т в час подойдут грануляторы серии ОГМ-1,5М российского производителя ALB Group. Все комплектующие этих грануляторов, кроме матриц, отечественного производства. Матрицы используются европейского производства – фирм General Dies (Италия), GRAF (Германия), Muench-Edelstahl. Одним из основных преимуществ этого оборудования является простота обслуживания, высокая ремонтопригодность и наличие запасных частей у большого количества поставщиков в России и странах СНГ.
К недостаткам оборудования этой фирмы относят недостаточное качество металла и несовершенство технологии сборки. Также можно использовать гранулятор «Грач-480», разработанный компанией «Невские Технологии – Инжиниринг». За его основу выбран серийно выпускаемый редуктор, который для обеспечения надежности номинально рассчитан на крутящий момент в 8–10 раз больше, чем требуется для прессующего узла при использовании 90 кВт двигателя. При разработке этого гранулятора конструкторы придерживались стандартизации комплектующих, используя гайки, шайбы, размеры под серийно выпускаемые метизы.
Еще один отечественный производитель – «Русский Гранулятор». Компания выпускает гранулятор НГК205РП, имеющий подвижные двойные ролики, производительностью 0,6 т/час и гранулятор НГК270РП (имеющий тройные подвижные ролики), производительностью 1000 кг в час.
Как отмечают в компании «Невские Технологии – Инжиниринг», участок гранулирования сухой стружки на предприятиях этой мощности окупается за год, при наличии оборудования для сушки опилок – за полтора-два года. В случае если оборудование будет работать на щепе, срок окупаемости составит два-три года. Применять в качестве сырья горбыль не рекомендуется – это потребует добавить в штат двух сотрудников, дисковую рубительную машину и дробилки щепы, что отрицательно скажется на прибыли компании.
Для пеллетных производств мощностью до 2,5 т в час рекомендованы грануляторы фирмы Muench RMP 520 (Германия) или «Грач-480». Сухая стружка на таких заводах обычно не используется либо ее доля мала, а основным сырьем служат влажные опилки и горбыль. При работе с опилками окупаемость оборудования «Грач-480» наступит через год-полтора. При работе с горбылем потребуется установить барабанную рубительную машину и дробилку щепы, что отодвинет срок окупаемости до полутора-двух лет. При покупке импортного оборудования срок окупаемости будет в полтора-два раза дольше.
Для заводов, производительность которых превышает 2,5 т в час, подойдет оборудование California Pellet Mill (США). Также можно использовать линии с Muench RMP 650 (или больше) или два гранулятора «Грач-480», Amandus Kahl, Andritz Sprout. Окупаемость этих прессов чуть быстрее, чем у оборудования предыдущей категории.
Инвестиции в производство гранул экспоненциально снижаются с ростом производственной мощности. Так же как и удельные затраты, например на заработную плату персонала. Если оператор линии гранулирования производит 1 т пеллет в час и получает зарплату 200 руб. в час, то стоимость заработной платы в себестоимости 1 т пеллет будет 200 руб. Если оператор линии, с той же часовой заработной платой, производит 15 т пеллет в час, то стоимость заработной платы в стоимости 1 т пеллет составит 200/15 – 12,33 руб.