Експорт деревних пеллет може стати привабливим напрямком для інвестицій.
Разом зі зростанням споживання цієї продукції в Європі, зростає і пропозиція нового обладнання для виробництва гранул.
- Продуктивність гранулятора залежить від кількості і діаметра отворів матриці, а також від її площі.
- Електрична потужність гранулятора в перерахунку на 1 т пелет, що випускаються повинна становити 70-100 кВт.
- На виробництво 1 т пелет витрачається 120-180 кВт / год, з них 60-80 кВт / год - на процес гранулювання.
Модельний ряд основного обладнання для виготовлення пеллет - грануляторів - як і перелік компаній-виробників, стає дедалі більшим, удосконалюються їх конструкції. На російському ринку свої розробки представляють, як вітчизняні виробники - ALB Group, «Невські Технології - Інжиніринг», «Русский Гранулятор», так і іноземні. Компанії Amandus Kahl GmbH & Co. KG (Німеччина) і California Pellet Mill Co (США / Нідерланди) виробляють преси потужністю від 500 кг до 5 т гранул на годину. Andritz Sprout A / S випускає обладнання для гранулювання потужністю 3,5 т на годину. Фірма Sweden Power Chippers AB (Швеція) являє гранулятори малої продуктивності - від 150 до 450 кг / год. Також гранулятори невеликої потужності, до 1 т на годину, виготовляє Радвилишкський машинобудівний завод (Литва). Німецький виробник Muеnch-Edelstahl GmbH випускає гранулятори потужність від 500 кг до 2 т на годину. Компанія AVS Slovakia, sro (Словаччина) поставляє гранулятори для деревини двох типорозмірів - потужністю 2 т за годину і 5 т на годину.
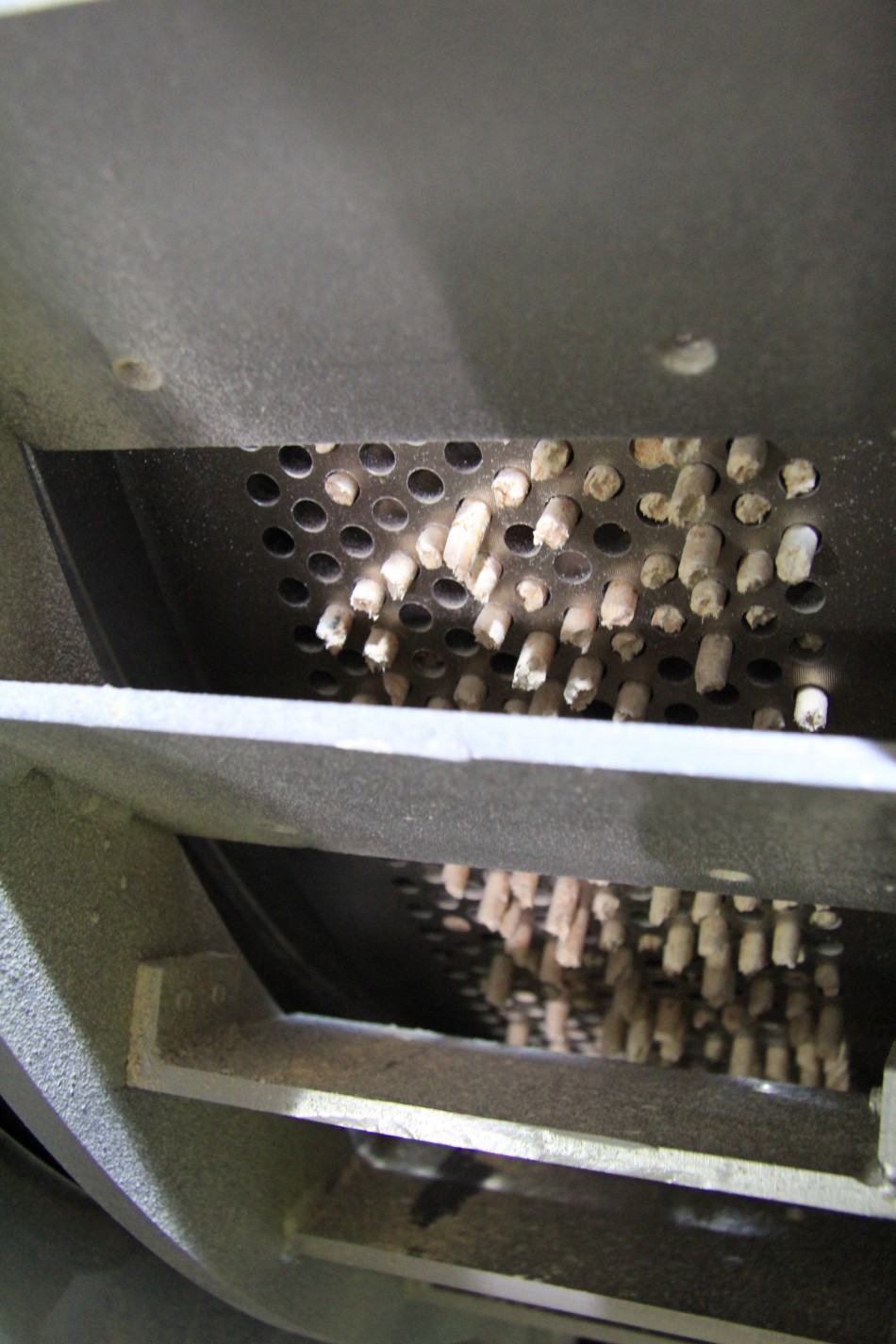
Також виробляють преси, але не постачають їх в Росію або тільки починають виходити на цей ринок, компанії: Salzhausener Maschinenbautechnik SALMATEC GmbH (Німеччина), LA MECCANICA srl (Італія), M • B • Z Mühlen (Німеччина), TRITEC GmbH (Німеччина) , Akademia2003 (Італія), Van Aarsen International Headquarters (Нідерланди), STOZA sro (Чехія), Gama Pardubice sro (Чехія), ZE.PI. SRL (Італія), General Dies Srl (Італія), Bliss Industries, Inc. (США), «Грантех» (Україна), Zhengchang Group Co., Ltd. (Китай), Bühler AG (Швейцарія).
Типи грануляторів
За конструкцією преси-гранулятори можуть бути з плоскою матрицею, з круглою матрицею, з двома вертикальними обертовими матрицями, гібрид гранулятора з плоскою і круглої матрицею. У грануляторах з плоскою горизонтальною матрицею, що обертається через отвори в ній матеріал продавлюється пресуючими вулицями і формується в гранули. Основними елементами преса є ролики, закріплені на приводному валу, і плоска матриця. Такі гранулятори невеликі за розміром, мають просту конструкцію, а тому підходять підприємствам з малим об'ємом переробки, а також приватним господарствам. До недоліків цього обладнання можна віднести те, що при певній окружній швидкості виникає віднесення матеріалу під дією відцентрових сил до периферії матриці і, як наслідок, нерівномірне навантаження на її робочу поверхню. Через різницю кутових швидкостей роликів відбувається нерівномірний знос поверхні матриці і роликів. Дуже складно домогтися однакового зазору між усіма роликами і матрицею. При виході з ладу одного підшипника в ролику, як правило, змінюються всі підшипники на роликовій голівці. Ремонт гранулятора з плоскою матрицею обійдеться дорожче, ніж гранулятора з круглою матрицею.
У грануляторах з круглою вертикальною матрицею, що обертається матеріал продавлюється через отвори матриці пресуючими вулицями і формується в гранули. У даній конструкції преса кожен ролик індивідуально підводиться до матриці, забезпечуючи необхідний зазор і тим самим найкращу якість одержуваного продукту, а також рівномірний знос роликів і матриці. Преси цієї конструкції найбільш поширені, на їх частку припадає близько 90% всього ринку грануляторів. Їх недоліком є велика окружна швидкість і, як наслідок, чутливість до вологості і фракції гранулюючого матеріалу, а також більше енергоспоживання.
Гранулятори з двома вертикальними, що обертаються в протилежних напрямках матрицями роликів не мають. Матриці розташовані так, що їх зовнішні діаметри накладаються один на одного, як левередж. Такі гранулятори не знайшли широкого застосування через високі експлуатаційні витрати і складнощі в роботі. Гібрид гранулятора з плоскою і круглої матрицею з'явився на ринку порівняно недавно. Такий прес-гранулятор 3000-200-10 представлений в Росії компаніями «ЛесІнТех» і Dieffenbacher (Німеччина). Устаткування поєднує в собі переваги пресів з плоскою і з кільцевою матрицею, при цьому виключаючи такі їх недоліки, як нерівномірність зносу матриць і роликів, довгий час їх заміни, відсутність візуального контролю за процесом гранулювання. Гранулятор розроблений для заводів великої продуктивності. Дана модель складається з десяти вузлів. Пресує вузол включає живильник, що пресує ролик і загальну плоску матрицю з заданим діаметром отворів.
Гранулятори з шестерним приводом найдешевші в експлуатації. У них немає великих втрат на тертя, як в пасовій передачі або в черв'ячній парі. У них найнижча вартість і витрата мастильних матеріалів. ККД одноступінчатої шестеренчатої передачі становить 98%, клиноременній - 96% і зменшується в процесі роботи (зносу ременів), ККД черв'ячної передачі становить 90%.
Гранулятори з клиноремінною і з шестеренчатою передачами однаково поширені. Переваги клинопасової передачі - велика стійкість до вібрацій і перевантажень камери гранулювання, які поглинаються за рахунок ременів і валів. У грануляторів з шестеренчатою передачею навантаження більше передаються на електродвигун. Щоб обладнання добре працювало, ремені повинні бути європейського виробництва, а це серйозно позначається на його ціні. При установці дешевих, менш якісних ременів шківи поміняють профіль, і навіть оригінальні ремені почнуть швидко зношуватися. Електроніка грануляторів за допомогою датчиків стежить за пробуксовуванням пасів, але на російських пелетних підприємствах ці датчики швидко забруднюються через низького рівня організацію праці і слабку підготовку кадрів. Термін служби клинопасової передачі становить близько 30 тис. Годин, але заміна ременів коштує недорого. Термін служби шестеренчатої передачі становить до 10 років, але вартість заміни дуже відчутна і може скласти до 50% вартості гранулятора. Дві перерахованих вище конструктивних ознаки є принциповими в класифікації конструкцій грануляторів.
Матриці для преса
Найбільш відповідальною детвллю, що зношуються є матриця гранулятора. Існує велика кількість їх різновидів. Якісно виготовлена матриця повинна поєднувати в собі високу опірність стирання, поломок і корозії, забезпечувати високу пропускну здатність для досягнення оптимальної продуктивності. Діаметр плоских матриць становить 100-1250 мм, товщина - 20-100 мм. Діаметр круглої матриці досягає 1000 мм.
Оскільки вартість матриць висока, на підприємствах приділяють велику увагу їх збереженню і правильній експлуатації. Матриці виготовляють з різних матеріалів. Головні вимоги до матеріалів - висока зносостійкість і пружність. Доброю зносостійкістю володіють матриці з нержавіючої сталі. Як правило, використовують сталь російського виробництва 40Х або сталі HARDOX 500 і 20CRMN. Використовувана сталь повинна бути зносостійкою і мати загартування 45-60 од. за шкалою твердості Роквелла.
За технологією виготовлення розрізняють зміцнені матриці з нержавіючої сталі, які можуть бути з вакуумної плавкою або з наскрізною загартуванням, а також науглероженні матриці з легованої сталі.
Отримання гранул правильної форми за допомогою безперервного пропуску сировини через перфоровані матриці в грануляторах досягається завдяки тиску валків і тертю сировини по металевим стінках отворів матриць. Чим довші ці отвори, тим тривалішим вплив тертя і тим міцніше виходять гранули. Між діаметром гранул і довжиною отворів матриці (довжина пресування) існує співвідношення, при якому виходить встановлена міцність гранул. Чим більше діаметр гранул, тим товщою повинна бути матриця. Перетин отворів в матриці дуже впливає на продуктивність гранулятора - чим він менше, тим менше продуктивність. Часто в отворах матриці робляться зенковки, щоб полегшити вхід продукту в отвори.
Товщина матриці повинна бути в 10 разів більше діаметру отворів. При виготовленні матриць товщиною менше 50,8 мм застосовують Цековки отворів, які полягають в тому, що свердлом розсверлюють верхні кромки отворів. Іноді роблять фаски на отворах. Так, матриці товщиною 50,8 мм можуть мати отвори розміром 4,8х38,1 мм з конусним поглибленням 12,7 мм. При цьому ефективна довжина освіти гранул складає 38,1 мм. Отвори для пресування гранул діаметром від 2,4 до 4,8 мм мають малу роззенковку у впуску. Отвори для гранул діаметром 9,5 мм і вище не тільки раззенковують, але і обробляють на конус до половини, а в деяких випадках і більше.
По виду каналів розрізняють матриці з прямими каналами, з роззенковкою на виході, з конусним виходом, з покроковим конічним виходом, з ключовим входом, з ключовим отвором. При недостатній товщині матриці гранула відразу ж руйнується. Розколювання деяких гранул по колу свідчить про те, що продукт недостатньо стискається або недостатній час витримується в матриці під тиском. Продуктивність гранулятора залежить від діаметра отворів матриці, їх кількості, площі матриці, а також якості шліфування внутрішньої поверхні отворів.
Поряд з матрицями на процес пресування великий вплив мають і ролики. Їх виготовляють із спеціальної загартованої сталі. На поверхні роликів є рифлення для зменшення ковзання і для захоплення гранулюючого матеріалу. Коли поверхня роликів зношується від тертя, що виникає при зіткненні з сировиною і матрицею, ролики проточують, знову нарізають рифл або замінюють. Зазвичай замінюють матрицю і ролики одним комплектом. Як і у ланцюгових пильних гарнітур (пари ланцюг - провідна зірочка), зношені ролики не ставлять до нової матриці, і навпаки, тому що поверхня зношених роликів зіпсує поверхню нової матриці. Матриця разом з роликами становить єдиний вузол, вони працюють спільно і вимагають правильної установки. Зазор між роликами і матрицею визначає ступінь стиснення. При нормальному розташуванні роликів від поверхні матриці виходять гранули необхідної міцності. Якщо зазор між роликами і матрицею збільшений, відбувається попереднє стиснення шару гранулюючої сировини, яке підвищує тиск в отворах матриці, і гранули виходять підвищеної твердості. У таких випадках матриці можуть повністю забиватися продуктом, і тоді робота гранулятора зупиняється.
Виробництво пелет розділяється на два етапи: перший - утворення попередньо стисненого шару сировини; другий - продавлювання сировини в отвори матриці і стиснення його завдяки тертю в отворах. Якщо ролики торкаються поверхні матриці, то тоді попереднього стиснення сировини не відбудеться, і з матриці будуть виходити м'які гранули або зовсім неспрессованний продукт.
Більш товстий шар попередньо стисненої сировини сприяє утворенню «мастила» між металом ролика і матриці, що зменшує знос матриці і валків. Занадто маленький зазор між роликами і матрицею дає тонкий твердий шар продукту, що не забезпечує необхідного захисту від зносу. У товстому шарі сировини поглинаються тангенціальні сили, що з'являються в результаті руху ролика по матриці і прагнуть загнути гострі кінці її отворів, забиваючи або пошкоджуючи поверхню шматочками металу. Товстий шар сировини, що попереджає передчасний знос і поломку матриці, слід застосовувати для забезпечення безаварійної роботи гранулятора.
Оскільки тертя в отворах матриці є важливим фактором отримання необхідного тиску і твердості гранул, нова матриця з шорсткими отворами, навіть при ретельній її обробці на заводі або при короткочасному зароблянні, дає дуже тверді гранули, а гранулятор показує низьку продуктивність. Надмірний тиск, що створюється підвищеним тертям в отворах нової матриці, можна компенсувати зазором між матрицею і роликами.
При виборі матриці гранулятора насамперед треба орієнтуватися на вид планованих до виробництва пелет. Однак фізико-механічні властивості деревної сировини, що безпосередньо впливають на гранулювання і багато в чому на характеристики одержуваних гранул, сильно варіюються в залежності від породи деревини і умов місця її зростання. Наприклад, час витримування в матриці, залежне від довжини каналу, впливає на якість гранул, особливо для хвойних порід. Витрати на енергію становлять значну частину собівартості гранул, тому матриці грануляторов часто характеризують таким показником, як см2 / кВт. В середньому на виробництво 1 т пелет витрачається 120-180 кВт / год, з них 60-80 кВт / год - на процес гранулювання. Вартість витратних матеріалів становить близько 100 руб. на 1 т, в залежності від сорту деревини та змісту піску.
Великий вплив на енергоємність процесу гранулювання, а також знос підшипників гранулятора надає ефективність системи мастила. Нещодавно на російському ринку з'явилися гранулятори фірми СРМ, на яких встановлені ролики з масляним мастилом, на відміну від звичайних - з змазкою. Система масляного змащення роликів (МСР) має ряд переваг, значно продовжує термін їх служби. В системі МСР масло циркулює по замкнутому контуру, забезпечуючи безперервну мастило роликів. Потік масла, що йде до кожного ролику, дозволяє безперервно контролювати температуру підшипників. Крім цього, закрита система запобігає потраплянню в ролики абразивів, так як відфільтрований потік масла видаляє частинки, що призводять до зносу підшипників, а також значно скорочує витрату мастила. Система МСР дозволяє знизити робочу температуру підшипників роликів на 35 ºС (з 135 ºС до 100 ºС) і збільшити термін їх служби на 7500 годин. Це призводить до річної економії понад 900 тис. Руб. на гранулятор.
Вибір гранулятора
При виборі гранулятора слід звертати увагу на його електричну потужність. У перерахунку на 1 т пелет, що випускаються ця цифра повинна знаходитися в межах 70-100 кВт. Як уже зазначалося, вона залежить від конкретної породи деревини. Для однієї і тієї ж породи, але з різних регіонів виростання цифра теж змінюється. Ще один важливий параметр - вартість основних змінних елементів гранулятора: матриць і роликів. Крім самої вартості, вибирається співвідношення вартість / ресурс. Крім того, мають велике значення терміни і процедури поставки запасних частин і витратних матеріалів.
Для невеликих пелетних цехів, чия виробнича потужність не перевищує 300 кг на годину, краще використовувати гранулятори з плоскою матрицею і простим охолоджувачем. Робочих примірників цього обладнання дуже мало, і стабільно вони працюють тільки на м'якій і сухій хвої (модрина). Сушилку тирси використовувати економічно недоцільно.
Для підприємства продуктивністю від 500 кг до 1 т на годину підійдуть гранулятори серії ОГМ-1,5 М російського виробника ALB Group. Всі комплектуючі цих грануляторов, крім матриць, вітчизняного виробництва. Матриці використовуються європейського виробництва - фірм General Dies (Італія), GRAF (Німеччина), Muench-Edelstahl. Одним з основних переваг цього обладнання є простота обслуговування, висока ремонтопридатність і наявність запасних частин у великій кількості постачальників в Росії і країнах СНД.
До недоліків обладнання цієї фірми відносять недостатню якість металу і недосконалість технології складання. Також можна використовувати гранулятор "Грач-480», розроблений компанією «Невські Технології - Інжиніринг». За його основу обраний серійний редуктор, який для забезпечення надійності номінально розрахований на крутний момент в 8-10 разів більше, ніж потрібно для пресу вузла при використанні 90 кВт двигуна. При розробці цього гранулятора конструктори дотримувалися стандартизації комплектуючих, використовуючи гайки, шайби, розміри під серійні металовироби, що випускаються.
Ще один вітчизняний виробник - «Русский Гранулятор». Компанія випускає гранулятор НГК205РП, що має рухомі подвійні ролики, продуктивністю 0,6 т / год і гранулятор НГК270РП (має потрійні рухливі ролики), продуктивністю 1000 кг на годину.
Як відзначають в компанії «Невські Технології - Інжиніринг», ділянка гранулювання сухої стружки на підприємствах цієї потужності окупається за рік, при наявності обладнання для сушки тирси - за півтора-два роки. У разі якщо обладнання буде працювати на трісці, термін окупності складе два-три роки. Застосовувати в якості сировини горбиль не рекомендується - це зажадає додати в штат двох співробітників, дискову рубільну машину і дробарку тріски, що негативно позначиться на прибутку компанії.
Для пелетних виробництв потужністю до 2,5 т на годину рекомендовані гранулятори фірми Muench RMP 520 (Німеччина) або «Грач-480». Суха стружка на таких заводах зазвичай не використовується або її частка мала, а основною сировиною служать волога тирса і горбиль. При роботі з тирсою окупність обладнання «Грач-480» настане через рік-півтора. При роботі з обаполком потрібно встановити барабанну рубільну машину і дробарку тріски, що відсуне термін окупності до півтора-двох років. При покупці імпортного обладнання термін окупності буде в півтора-два рази довше.
Для заводів, продуктивність яких перевищує 2,5 т на годину, підійде обладнання California Pellet Mill (США). Також можна використовувати лінії з Muench RMP 650 (або більше) або два гранулятора «Грач-480», Amandus Kahl, Andritz Sprout. Окупність цих пресів трохи швидше, ніж у устаткування попередньої категорії.
Інвестиції у виробництво гранул експоненціально знижуються з ростом виробничої потужності. Так само як і питомі витрати, наприклад на заробітну плату персоналу. Якщо оператор лінії гранулювання виробляє 1 т пелет на годину і отримує зарплату 200 руб. в годину, то вартість заробітної плати в собівартості 1 т пелет буде 200 руб. Якщо оператор лінії, з тієї ж годинної заробітної платою, виробляє 15 т пелет на годину, то вартість заробітної плати у вартості 1 т пелет складе 200/15 - 12,33 руб.