Принципиальная схема производства топливных гранул из биомассы.
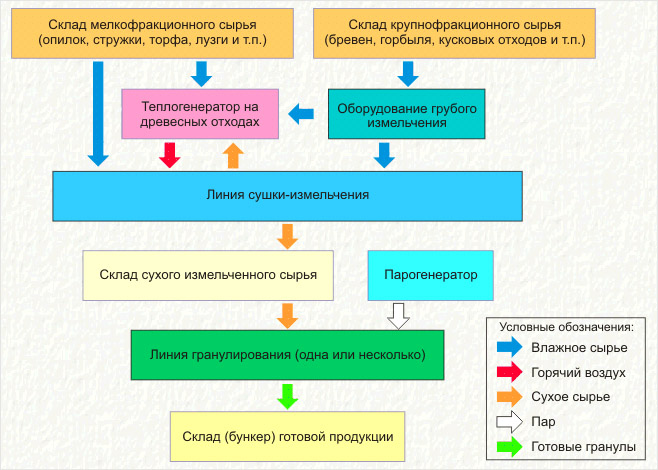
Пояснения:
1. На данной схеме изображен принцип работы пеллетного или брикетного производства на любом виде сырья. В каждом частном случае необходимость применения и количество элементов оборудования каждого типа определяется:
а) конкретным видом используемого сырья;
б) производительностью завода;
в) Вашими пожеланиями.
Примеры: а) при использовании сырья с влажностью до 12% (такого, как лузга подсолнечника или сухие стружки), линия сушки и теплогенератор не нужны;
б) при общей производительности завода 4 т/ч линий гранулирования может быть одна или две; в) приобретение оборудования склада сухого сырья и бункера готовой продукции определяется только Вашим желанием.
2. При использовании для производства тепла природного газа - теплогенератор на древесных отходах не нужен. При использовании теплогенератора на древесных отходах желательна организация возврата части высушенного сырья для сжигания в теплогенераторе, это значительно увеличивает его КПД и возможность регулировки тепловой мощности.
3. Парогенератор увеличивает производительность линии гранулирования на 20 ... 25%, уменьшает износ матрицы, улучшает качество гранул.
Данный комплекс предназначен для приемки, накопления, дозированной подачи, сушки, измельчения и гранулирования продуктов растительного происхождения (биомассы).
Технологический процесс
Далее описан наиболее полный процесс. В случае отсутствия необходимости применения какой-либо его части (например, процесса сушки или дробления) данная часть описания может быть опущена.
Завод в такой комплектации может производить гранулы практически из любого растительного сырья (биомассы) влажностью не более 50%.
При более высокой начальной влажности сырья завод комплектуется дополнительно оборудованием механического отжима избыточной влаги (декантером).
Бревна, горбыль и т.п. древесные отходы подаются в рубильную машину (21) транспортером (22). Из нее щепа попадает в транспортер (23) и далее - на механизированный склад “подвижный пол” (1).
Мелкофракционное сырьё подвозится автотранспортом (либо погрузчиком) и ссыпается на механизированный склад “подвижный пол” (1).
Стокеры подвижного пола имеют гидравлический привод и под его действием совершают возвратно-поступательные движения. Лопатки (“крылья”) стокеров имеют клиновидную форму, поэтому при движении стокеров сырье с регулируемой скоростью подачи направляется к цепному (скребковому) транспортеру (2), далее сырье подается на дисковый сепаратор (3). На нем от сырья отделяется камни, коренья и т.п. примеси, которые попадают в переносной контейнер (на схеме не показан), а сырьё через самотёк попадает в загрузочную секцию Агрегата Сушки-измельчения (4).
Сюда же подаются продукты горения из теплогенератора (5) и засасывается холодный атмосферный воздух через аварийно-растопочную трубу (6). Первоначально смешиваются продукты горения и холодный воздух. Пропорция смешивания регулируется автоматически, что обеспечивает поддержание заданной температуры теплоносителя. Затем теплоноситель смешивается с влажным сырьем и засасывается в Агрегат Сушки-измельчения (4).
В нем сырье измельчается и затем высушивается, поднимаясь в потоке теплоносителя к динамическому классификатору, находящемуся в головной секции Агрегата Сушки-измельчения. Динамический классификатор, частота которого задаётся с пульта управления (20), пропускает мелкое и сухое сырье, а крупные и влажные частицы сырья возвращает к ротору Агрегата. Этот процесс повторяется до получения необходимой влажности и степени измельчения сырья. Подробнее о принципах работы и характеристиках АС можно посмотреть здесь.
Измельчённое и высушенное сырьё (с этого момента его принято называть мукой) засасывается в осадочный циклон (8) за счет разряжения, создаваемого дымососом. В циклоне мука осаждается за счет центробежной силы и двигается вниз, а отработанный теплоноситель выбрасывается в дымовую трубу (19).
Из циклона мука через шлюзовой затвор подаётся в шнековый или цепной транспортер (9), далее поступает в бункер гранулятора (10). Внутри бункера находится устройство, препятствующее слеживанию муки. Из бункера мука подается шнековым питателем с регулируемой скоростью подачи в смеситель (кондиционер) пресса, сюда же подается вода (либо пар). В смесителе происходит кондиционирование продукта, т.е. доведение влажности муки до уровня, необходимого для процесса гранулирования. Из смесителя увлажненная мука через отделитель ферромагнитных примесей выводится в пресс-гранулятор (11).
В камере прессования гранулятора мука затягивается между вращающейся матрицей и прессующими вальцами и продавливается в радиальные отверстия матрицы, где под действием большого давления происходит формирование гранул. Выдавленные из отверстий гранулы наталкиваются на неподвижный нож и обламываются. Обломанные гранулы падают вниз и через рукав кожуха выводятся из пресса.
Гранулы, выходящие из пресса, имеют высокую температуру и непрочны, поэтому они транспортируются вертикальным транспортером - норией (12) в охладительную колонку (13). Здесь через слой гранул вентилятором циклона (16) всасывается воздух, который охлаждает гранулы и одновременно отсасывает часть несгранулированной муки в циклон. В процессе охлаждения влажность гранул уменьшается за счет испарения влаги, и в гранулах происходят физико-химические изменения. В результате они приобретают необходимую твердость, влажность и температуру. Из охладительной колонки, по мере ее наполнения, гранулы поступают на сортировку (14), где происходит отделение кондиционных гранул от крошки.
Гранулы выводятся через выгрузную горловину и подаются на норию готовой продукции (15), а крошка отсасывается в циклон (16) и далее направляется вместе с мукой на повторное прессование. Норией готовой продукции гранулы подаются в бункер готовой продукции (17). На нем расположен дозатор. Под этим бункером расположены электронные весы (18), а на стойках бункера имеются крючки для вывешивания большого мешка (биг-бэга). Также вместо биг-бегов может производиться расфасовка гранул в 15 кг. полиэтиленовые мешки, которые складываются на поддон. Заполненные биг-беги или поддоны с мешками погрузчиком или гидравлической тележкой транспортируются на склад готовой продукции.
Теплогенератор в данной комплектации может загружаться топливом как в ручном (через дверцу), так и в автоматическом режиме - из бункера топлива (7). Пополнение бункера топлива происходит автоматически за счет возврата части муки от осадочного циклона (8) системой пневмотранспорта (24). Опционально бункер топлива может пополняться дополнительным транспортером со склада сырья или отдельного склада топлива (на схеме не показаны).
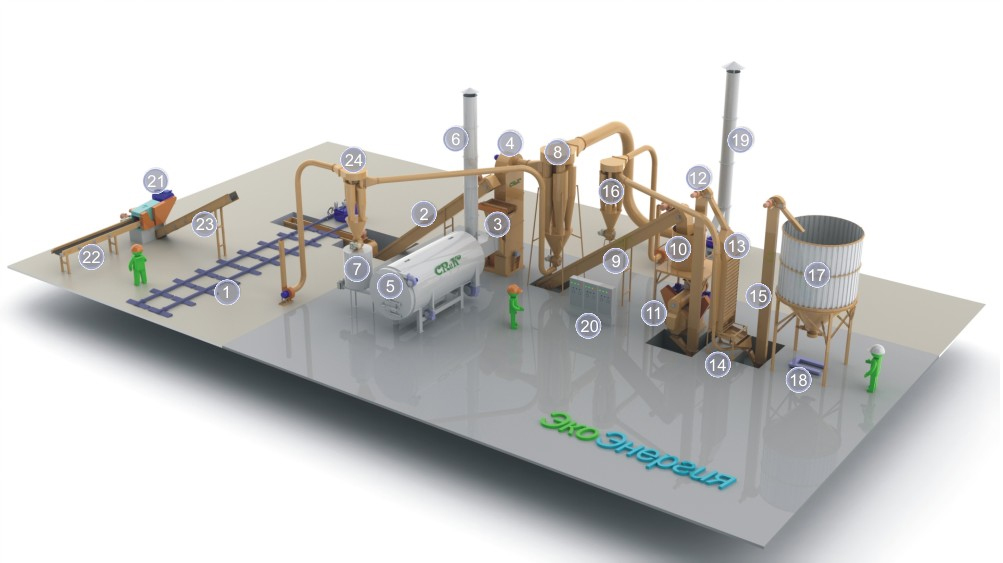