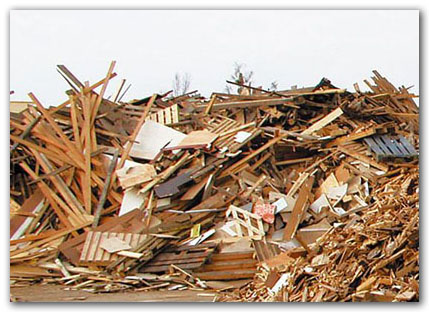
Котельні являють собою установки повної заводської готовності або комбінації з модулів заводського виготовлення і конструкцій, що монтуються безпосередньо на майданчику замовника. Стандартний обсяг поставки включає в себе транспортери палива, пальники, котел, пристрій для очищення димових газів, трубопроводи, КВП і будівля для паливного складу і котельної установки. Паливний склад оснащений гідравлічними рейковими розвантажувачами. Паливо подається по ланцюговим конвеєрам в бункер для палива, що знаходиться в котельному приміщенні, і далі за допомогою шнека паливо подається знизу в передню топку через отвір, наявний в середині решітки. Рівномірна подача і ефективна сушка палива забезпечені тим, що паливо не перемішується з висушеним або палаючим паливом завдяки обертанню секцій решітки. Передня топка і камера догорання мають вогнетривку футеровку. Завдяки теплопередачі футеровки забезпечується рівномірність і ефективність згоряння навіть при використанні біологічних мас з вологістю до 65%.
Потужність і викиди.
ККД подібних установок знаходиться в межах від 84 до 88,3% і залежить від застосовуваного навантаження. Мінімальне навантаження складає 20%, їй відповідає ККД 84%, далі зі збільшенням навантаження ККД різко зростає і досягає 87,8% при навантаженні 50%, потім ККД плавно збільшується до 88,3%.
Зменшення ККД за високої вологості (до 65%) кори і тирси доведено до мінімуму за допомогою ефективної утилізації тепла (низька температура димових газів) і невеликої витрати повітря у всьому діапазоні потужностей.
Витрата палива залежить від виду палива і його вологості. Для приблизної оцінки можна вважати, що для котельні 1 МВт необхідно 2 м3/год при вологості палива 60-65% і 1,5 м3 / ч при вологості 40-45%.
Викиди димових газів з вмістом кисню 4% можна визначити наступним чином:
NO2 | 120 | mg/MJ палива |
CO | 120 | mg/MJ палива |
Тверді речовини |
50, 100 or 200 1) | mg/MJ палива |
Неодноразові випробування спалювання кори, тирси та сумішей пакувальних відходів, лушпиння від зернових культур, кускового торфу і біологічного мулу деревообробної промисловості в суміші з корою і тирсою показали дуже низькі рівні викидів вуглеводнів, поліциклічних ароматичних вуглеводнів, поліхлорованих дибензо-п-діоксинів і-фуранів, а також важких металів. Навіть при самих строгих нормах за викидами в котельні можна спалити суміші цих відходів і біологічних мас.
Таблиця 1. Викиди звичайних компонентів димових газів
Паливо: | Кора + тирса (відходи) | Відходи + мул | Відходи + енерг. культури | Відходи + упак. відходи |
Потужність котельні МВт | 2,82 | 2,12 | 3,01 | 1,5 |
O2, % по масі | 4,3 | 4,4 | 4,7 | 5,4 |
Горючі речовини | 20 | 13 | 13,3 | 15 |
У золі, % по об'єму | ||||
Летюча зола, мг/m3n, O2=6% (сухі гази) | 262 | 254 | 131 | 170 |
CO | 15 | 11 | 18 - 315 | 11 |
NO, В вигляді NO2 | 235 | 373 | 339 | 242 |
SO2 | 6 | 40 | 7,5 | 6 |
HCl | 3 | 3 | 3 | 7 |
Спалювання різних горючих відходів можливо за принципом спалювання суміші. Це означає, що припустима частка підмішуваного палива складає не більше 30% від частки основного палива.
Вироблення електроенергії
Вироблення електроенергії в невеликій кількості, на основі використання пару, можна поєднати з виробництвом теплової енергії. Основна мета - замінити частину або всю електроенергію, що купується. Така інвестиція підходить найкраще для виробничого підприємства невеликої потужності, наприклад, для лісопильного заводу чи іншого деревообробного процесу, який потребує одночасно як в електроенергії, так і теплової енергії.
Співвідношення вироблення електроенергії до теплової енергії залишається невеликим (бл. 15%) через невисокі параметрів пари. Типові діапазони потужності на невеликих заводах складають від 0,4 до 1,2 МВт / електрику і від 3 до 8 МВт / тепло.
Можливе дистанційне керування роботою установки.
Термін окупності інвестицій котельні при деревообробному підприємстві становить від 3 до 5 років і залежить від витрат підприємства на закупівлю енергії, які будуть зекономлені, а також від розмірів інвестиційних витрат.
Якщо підприємство використовує теплову енергію не тільки для своїх сушильних цехів, але і для теплофікації, термін окупності скорочується на 20%.