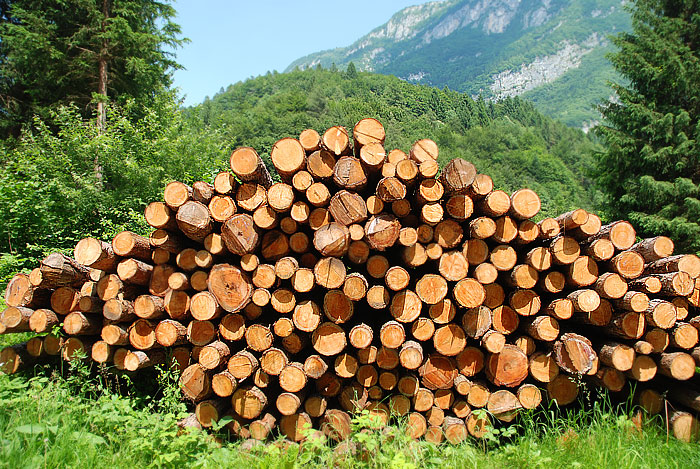
За способом пресування кінцевий продукт поділяється на гранули та брикети.
Беручи участь у міжнародних виставках та різних зустрічах, стало зрозуміло, що переважна маса потенційних споживачів обладнання з переробки рослинних відходів має дуже туманне уявлення про плюси й мінуси того чи іншого методу утилізації рослинних відходів.
Гранули виходять завдяки продавлюванню тирси через фільтри діаметром 6-8 мм. Брикети можуть виходити прямим пресуванням на гідравлічному або механічному пресі. Крім того, можна використовувати метод шнекового пресування, коли продукція виходить безперервно (як на м'ясорубці).
Існує думка, що за кордоном користуються великим попитом тільки гранули. Однак, попит на паливні брикети в Європі також постійно високий, ціни на нього безперервно ростуть і вони в 1,5 рази більше, ніж вартість гранул. Брикети, виконані методом шнекового пресування, більш переважні для покупців в порівнянні з простим пресуванням, та й дорожче майже в 2 рази.
У Європі на паливні гранули та брикети діють стандарти, у яких дуже високі вимоги щодо зольного залишку. Так стандарт Швеції на брикети SS 18 71 21 для другої групи якості вимагає зольність не вище 1,5%, а для першої групи не вище 0,8%. Вже є випадки штрафних санкцій нашим постачальникам за перевищення зольності. Вже часто замовники з Європи запитують, який метод сушіння, заперечуючи сушку безпосередньо димовими газами.
Далі проведемо коротке порівняння переваг та недоліків виробництва гранул та брикетів (брикетів, виконаних шнековим пресуванням).
Обладнання для виробництва гранул більш складне і, звичайно, більш дороге. Ремонти такого обладнання так само порівняно дорогі і виконати ремонт можна тільки на заводах-виробниках. Можна перерахувати підприємства, які зазнають величезні труднощі через це.
У технічній літературі визнано, що найкращі показники за питомими капітальними витратами є шнекові преса.
Вузьким місцем у пресі - це шнек, який в даний час виробляє близько 100 тонн брикетів і потребує заміни. Заміна шнеків - проста операція, яка виконується за 10 - 15 хвилин. Ціна нової шнекової насадки близько € 50, реставрація на порядок дешевше і може виконуватися в простих майстернях, де є електрозварювання.
Вимоги до сировини, тобто до тирси, у гранул більш високі, ніж у брикетів. Потрібен додатковий тонкий помел. Не допускаються помітні домішки кори.
При шнековому пресуванні вимоги до тирси значно менш суворі. Велика стружка, окремі шматочки довжиною до 20 мм, кора, хвоя - все це не заважає роботі пресу.
Економічно виправданим при виробництві гранул є продуктивність не менше 1,5 тонни на годину за виходом, тобто на вході треба мати як мінімум 6-8 м куб. тирси на годину. Такий обсяг виробництва тирси характерний для порівняно великих комбінатів. Для невеликих ділянок таке обладнання і недоступне і не буде забезпечене сировиною.
Гранули механічно неміцні, але все частіше покупець звертає увагу на крихти в герметичній тарі (біг-бегах), які утворюються при необхідних перевантаженнях гранул при транспортуванні (таких перевантажень виявляється 6-8). Той же шведський стандарт вимагає, щоб відсів крихти у покупця не перевищував 0,8%. Дуже великий попит зобов'язує європейських покупців поки припустимо ставитися до цього недоліку.
Брикет, отриманий методом шнекового пресування, крім високої щільності (1,1-1,2 т / м куб.) має зміцнюючу шкоринку на поверхні. Брикети практично не дають крихти і можуть транспортуватися в два яруси. Шкоринка на поверхні зменшує проникнення вологи в брикет.
В даний час ведуться роботи з розробки конструкцій для механізованої подачі брикетів в топки теплових станцій. Автоматична різка брикетного рукава на виході на довжину 60-70 мм дозволяє використовувати звичайні гвинтові конвеєри. Вдале рішення цього питання, а проект, очевидно, буде реалізований, різко розширить ринок брикетів.
Важливою проблемою є сушіння вихідних матеріалів до необхідних 8-12% вологості. Просте й економічно виправдане рішення дозволило б різко збільшити випуск і гранул і брикетів.
Повітря для сушіння матеріалу необхідно нагріти. Іноді використовується мазут (італійські установки), дизельне паливо (установки східної Європи), гас (японські установки). Деревні відходи, безумовно, економічно найбільш привабливі як паливо.
Повітрянагрівальні установки, що працюють на деревних відходах, можуть мати дві принципові схеми: димові гази потрапляють прямо у відділення сушіння або димові гази проходять через теплообмінник й у відділення сушіння потрапляє чисте нагріте повітря. Кожна з цих схем має і плюси і мінуси.
При прямій подачі топкових газів в сушильне відділення між газом та тирсою велика різниця температур, що підвищує ефективність сушіння. Однак висока температура створює небезпеку пожежі. Димові гази, охолоджуючись, залишають у тирсі багато сажі, що підвищує залишкову зольність матеріалу.
При проходженні димових газів через теплообмінник проблема загоряння тирси практично знімається. Немає осадження сажі. Однак температуру на вході в сушильне відділення не можна підняти вище 2000С. Повітрянагрівальних установок, що працюють на деревних відходах і подають повітря через теплообмінник, установної теплової потужності вище 500 кВт поки немає.
Як зазначено вище, економічно виправданим для гранул є випуск не менше 1,5 т/год.
Відомі шнекові преса австрійської фірми Pini-Kay, що випускаються вже кілька десятків років, мають продуктивність близько 400 кг/год. Для сушіння 400 кг/год за виходом потрібна теплова потужність близько 400 кВт. Отже, схема з використанням повітрянагрівальної установки тепловою потужністю до 500 кВт з теплообмінниками в комплекті зі шнековими пресами виявилася оптимальною.
У ініціативному порядку в Білорусії група ентузіастів протягом декількох років терпляче, вузол за вузлом, відпрацьовували технологічну схему лінії з переробки рослинних відходів у паливні брикети. В основу був узятий принцип шнекового пресування і прототипом став прес фірми «Pini-Key». Цей прес найбільш вдало проявляє себе вже кілька десятків років. Однак у прес внесено багато удосконалень. Зокрема, введена система підстроювання пресу залежно від складу матеріалу, що пресується, проведено математичне моделювання процесу пресування для вибору профілю каналу пресування, значно зменшено вагу.
Інший важливий блок лінії - це сушка тирси до необхідної вологості. Сушіння здійснюється в двоходовому сушильному барабані з імітацією «киплячого шару» при вхідній температурі повітря близько 180-200 С.
Для переробки вихідних матеріалів до необхідної фракційності встановлюється автоматична різка.
Дуже заманливо переробляти деревні відходи в тріску безпосередньо на лісових ділянках, але для цього потрібна доступна й дешева електроенергія. Вже зараз можна запропонувати в комплекті з тріскорізкою електрогенератор в комплекті з газогенератором, що працює на відходах деревини.
Вже зараз реалізується лінія 3-го покоління, у складі якої блок діагностики технологічних процесів з вимірами в реальному часі вологостей та витрати матеріалу та повітря, що допомагає в роботі оператора.
При контактах з виробничниками завжди до нашої лінії проявляється величезний інтерес, дуже багато питань, загальних і конкретних, а також виражалося здивування, що такі технічно оснащені та порівняно дешеві лінії вже створені в Білорусії.
Удосконалення конструкцій вузлів триває.