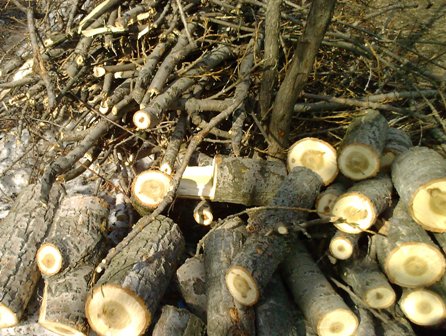
1. Зміна розмірів частинок вихідної сировини для гранулювання
Перед тим як почати гранулювання, незалежно від використовуваного вихідного матеріалу ( деревини, соломи тощо), необхідно отримати частинки одного розміру. Неоднорідність сировини, а саме, включення частинок крупного або навпаки, дрібного розміру можуть значно вплинути на якість пелет. Саме це, до речі, і є фактором, що перешкоджає широкому поширенню невеликих прес-грануляторів. Справа в тому, що в невеликих пресах відсутня ділянка підготовки сировини, де і відбувається приведення сировини до одного розміру, тому при використанні подібних грануляторів необхідно використовувати одне стабільне джерело сировини, або перебудовувати гранулятор з кожною новою партією тирси, що не завжди економічно вигідно.
2. Зміна вологості вихідних матеріалів
Однією з причин популярності пелет є їх низька (нижче 10%) вологість, що веде до високої ефективності їх застосування і практично повної відсутності диму при спалюванні. У свою чергу, при виробництві пелет необхідно правильно підібрати вологість вихідної сировини, згідно з деякими даними, при вологості сировини 11-12% готові пелети кришаться і не можуть бути використані для опалення, аналогічний ефект спостерігається і при вологості менше 5 %. Таким чином, якщо ви не контролюєте вологість вихідної сировини, ви не контролюєте процес виробництва. З іншого боку, кожен % зменшення вологості це додаткові витрати на сушку.
3. Використання наповнювачів і покращувачів
Незважаючи на те, що більшість західних стандартів забороняють використання присадок для виготовлення пелет (пелети просуваються на ринок як екологічно чисте паливо), добавка деяких натуральних субстанцій дозволяє поліпшити їх якість. Крім того, можливо підібрати оптимальне поєднання різних вихідних матеріалів (наприклад, частина сировини твердих порід дерева, а частина – м'яких).
4. Зміна швидкості подачі сировини в гранулятор
Деякі виробники з метою отримання максимального прибутку починають подавати сировину в прес на максимальній швидкості, що веде до зниження якості вироблених пелет. Необхідно (часто тільки методом проб і помилок) підібрати оптимальну швидкість подачі пелет та суворо дотримуватися її в процесі виробництва. Навіть невелика зміна швидкості загрожує перегрівом матриці і, як наслідок, виходом її з ладу. Швидкість подачі пелет строго індивідуальна для кожної лінії і варіюється навіть для прес грануляторів одного виробника.
5. Зміна в умовах кондиціонування
Під кондиціюванням в даному випадку ми розуміємо додаткову підготовку вихідної сировини перед тим, як вона досягне прес гранулятора. Процес може включати в себе використання пари, яка використовується для розігріву сировини і початку активації природного клею лігніну. Технологія кондиціювання суто індивідуальна і рекомендується до використання не на всіх виробництвах.
6. Зміна температурного режиму
Температура, на думку багатьох виробників, є ключовим чинником, що впливає на виробництво пелет. До того моменту поки не досягнута певна температура, натуральний лігнін не проявляє своїх клеючих властивостей, і випуск пелет неможливий, з іншого боку, висока температура може завдати шкоди обладнанню (гранулятор, матриця, ролики). Непрямим індикатором може служити колір і "матовість" пелет, що випускаються.
7. Зміна розташування роликів і матриці
Зміна зазору між роликами і матрицею веде не тільки до зміни швидкості зносу витратних матеріалів, але і до зміни якості випущених пелет, а також до зміни енерговитрат на виробництво пелет. Правильно виставлений зазор значно збільшує термін життя матриці. При заміні матриці на аналогічну за розмірами, але виготовлену з іншого матеріалу необхідно провести пере переналаштування гранулятора, як і при заміні роликів на ролики з іншим "малюнком".
8. Зміна швидкості гранулювання
Цей параметр пов'язаний зі швидкістю подачі вихідної сировини (більше сировини в одиницю часу, вище швидкість обертання роликів матриці), проте деякі матеріали при рівній швидкості подачі тирси потребують більшого часу для гранулювання.