Схема завода производства топливных брикетов на базе сушилки "АС-4" и пресса "C.F.Nielsen" BP6500
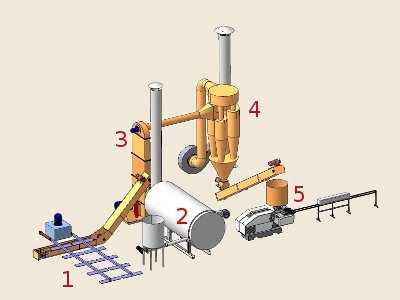
Опилки с пилорамы загружаются в склад "подвижное дно" (1). Крупные отходы (горбыль, обзол) с помощью рубильной машины (на схеме не обозначена) перерабатываются в щепу и с помощью отводящего транспортера поступают туда же. Из склада "подвижное дно" опилки и/или щепа естественной влажности подаются в агрегат сушки/измельчения АС-4 (3). Нагретый с помощью теплогенератора (2) воздух в необходимом количестве также подается в АС-4 и участвует в процессе сушки. На выходе АС измельченная и высушенная до необходимой влажности (задается с пульта) фракция осаждается в циклоне (4), отработанный теплоагент через дымосос отводится наружу. Сухое сырье после циклона с помощью шнекового транспортера поступает в бункер (5), оснащенный ворошителем и дозатором для подачи в оконечное оборудование прессования.
Преимуществами данной схемы является простота, компактность и относительно низкая цена.
О недостатках читайте в тематических разделах сайта по составным узлам такого завода: сушилке, теплогенератору и системе управления и автоматики, где подробно описано почему мы не рекомендуем использовать это оборудование с импортными автоматическими брикетными прессами.
Следует отметить, что такой цикл возможен только с применением указанного выше оборудования. Другие типы сушилок, например барабанная, требуют наличия двух дробилок для измельчения сырья на входе и выходе сушильного барабана, что усложняет и удорожает весь участок подготовки сырья.
С другой стороны, построение сушки на основе барабана дает 100% надежный результат, предсказуемость, а также возможность полной автоматизации и контроля над всеми процессами, что гарантирует стабильную работу любого пресса.
Торф
Схема выше показана для наиболее частого примера - переработка древесных отходов от пилорамы. Основные ее узлы применяются и при прессовании другого сырья.
Торф обычно поступает в виде равномерной волокнистой фракции с встречающимися в ней плотными комками. Относительная влажность составляет обычно порядка 50-60%. В составе линии в этом случае входят склад "подвижное дно", куда разгружается привезенный торф, сушилка-измечитель АС-4 с теплогенератором. Теплогенератор в этом случае работает на торфе.
На заводе изготовителе многократно проводились испытания по сушке торфа на "АС", всякий раз сушилка справлялась с заданием, однако все тесты былм кратковременными и о долговременных результатах судить пока рано.
Солома
Солома обычно находится в больших тюках или рулонах. В принципе, солома подсыхает при заготовке естественным путем и этапа сушки можно избежать, если позаботиться об этом на этапе заготовки - своевременно убирать в сухой склад, накрывать тюки на полях. В этом случае главную проблему составляет измельчение соломы до необходимой фракции. Обычно для этого используют шредер, который режет солому кусками 5-10 см, затем молотковую дробилку, которая домалывает фракцию.
Лузга подсолнечника и другие с/х отходы
Обычно готовы к прессованию "как есть".
http://bioresurs.com